
Logistica delle bevande: come fa la Coca-Cola ad arrivare nella bottiglia e al consumatore?
Economia e logistica
Alla Coca-Cola la produzione è sicura, pulita e automatizzata. E anche la consegna rispetta standard rigorosi. Per questo l'azienda, per il trasporto a corto raggio pesante, punta solo sugli autocarri Mercedes-Benz.
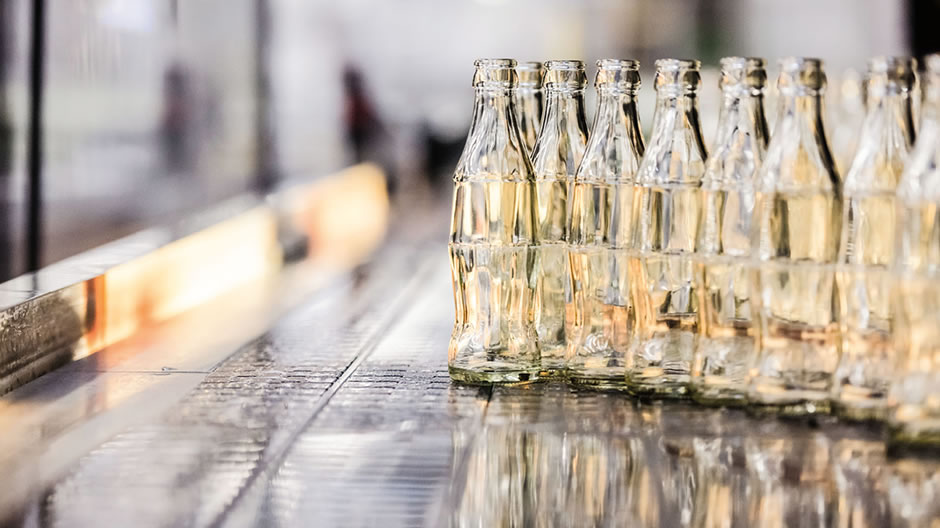
Pulizia perfetta. Restituite, pulite, pronte per il prossimo giro: a Hildesheim si riempiono fino a 46.000 bottiglie l'ora.
Fa parte della colonna sonora di ogni estate: il rumore del frigorifero che si apre, delle bottiglie di vetro, del tappo a corona che salta. La Coca-Cola ghiacciata nella bottiglietta da 0,2 litri è un vero classico. «Mercedes-Benz Transport» ha raggiunto il suo luogo d'origine, per poi accompagnarla nel suo viaggio. Che comincia, per esempio, a Hildesheim: qui si trova una delle 16 sedi produttive di Coca-Cola Deutschland. I circa 500 collaboratori dello stabilimento fanno sì che le cinque linee di produzione riempiano bottiglie 24 ore su 24. L'obiettivo di quest'anno: imbottigliare un milione di litri al giorno.
Nella sala enorme si sentono rumori di ogni tipo. Il direttore di questa orchestra è Alexander Haferkamp: il responsabile della produzione, 35 anni, deve avere tutto sotto controllo. I vuoti riconsegnati sono sufficienti? Quanto dura ancora la riserva di sciroppo? Per quale misura di bottiglie bisogna preparare gli impianti? Tutti i macchinari vengono monitorati, le anomalie di funzionamento e le irregolarità protocollate con precisione. I meccanici sono sempre pronti a intervenire per ridurre al minimo i tempi di fermo. Per il team di Haferkamp, che ha studiato da mastro birraio, ogni giorno è diverso dall'altro.
Processi ben armonizzati.
Per la bottiglia piccola di Coca-Cola invece il percorso è sempre lo stesso. Arrivate allo stabilimento, bottiglie e casse vengono separate, lavate e smistate. Due addetti raccolgono dal nastro trasportatore le bottiglie di forma diversa. Nella fase successiva devono essere eliminati dalla bottiglia eventuali corpi estranei. Poi si prosegue verso l'impianto di lavaggio: «Le bottiglie sono immerse in due diverse soluzioni detergenti a 80 gradi Celsius, una dopo l'altra, e vengono risciacquate con acqua pura. Poi la bottiglia è assolutamente pulita», spiega Haferkamp. In seguito è il turno dell'«ispettore», un apparecchio che esegue una scansione di tutte le bottiglie per non farsi scappare nemmeno il minimo danno.
Solo dopo arriva il momento decisivo: nell'impianto di riempimento, la Coca-Cola finisce nella bottiglia. In precedenza la bevanda è stata miscelata in serbatoi anonimi in una sala secondaria, con acqua potabile, sciroppo – dalla ricetta rigorosamente segreta – e naturalmente anidride carbonica.
L'imbottigliatore dell'impianto di riciclaggio riempie tra 40.000 e 46.000 bottiglie l'ora. «È il cuore della linea di produzione e segna il ritmo per tutto il resto: le prestazioni degli altri macchinari della produzione dipendono dalla quantità di bottiglie riempite», spiega il direttore di produzione Haferkamp. In base alla velocità, per esempio, ogni secondo undici bottiglie vengono etichettate e tappate, prima di essere sottoposte a un ultimo controllo di qualità e arrivare nelle casse gialle pulite.
Questo articolo contiene materiale informativo aggiuntivo (video, immagini e reportage, ecc.) riservato agli utenti registrati. Per avere accesso illimitato all'articolo esegui il login con il tuo account RoadStars o registrati gratuitamente.
Diventa una RoadStar e accedi a contenuti e iniziative esclusivi!
Login per utenti registrati RoadStars
Non sei ancora registrato? Iscriviti adesso a RoadStars
Ottieni l’accesso esclusivo a eventi e attività emozionanti, che solo RoadStars può offrire.
Iscriviti a RoadStars«Il cliente si aspetta la merce giusta, nella quantità giusta, al momento giusto e con la qualità giusta. Perciò il buon funzionamento della logistica delle consegne ha un'importanza estrema.»
– Francis Driessen, responsabile della logistica di rete per gli stabilimenti di Achim e Lüneburg
Ora la Coca-Cola esce dalla sala di produzione a gruppi di 40 casse. Nello stabilimento di Hildesheim ogni bottiglia viaggia per circa un'ora sui nastri trasportatori. Dal confezionamento su pallet si va al magazzino, e da qui direttamente ai clienti o ai centri di distribuzione nella regione.
«124 giorni senza incidenti sul lavoro. Periodo più lungo senza incidenti: 370 giorni.» Il cartello all'ingresso del magazzino di consegna ad Achim, vicino a Brema, non lascia dubbi: per la Coca-Cola Deutschland la sicurezza è importante. Non c'è da stupirsi allora se la flotta di 17 veicoli è costituita in gran parte da autocarri Mercedes-Benz. «Il cliente si aspetta la merce giusta, nella quantità giusta, al momento giusto e con la qualità giusta. Perciò il buon funzionamento della logistica delle consegne ha un'importanza estrema», spiega Francis Driessen, responsabile della logistica di rete per gli stabilimenti di Achim e Lüneburg. Per averne conferma basta uno sguardo al magazzino, in funzione dal 2017: tutto è mantenuto rigorosamente pulito e ordinato. Se qualcosa si rompe, i cocci scompaiono in quattro e quattr'otto.
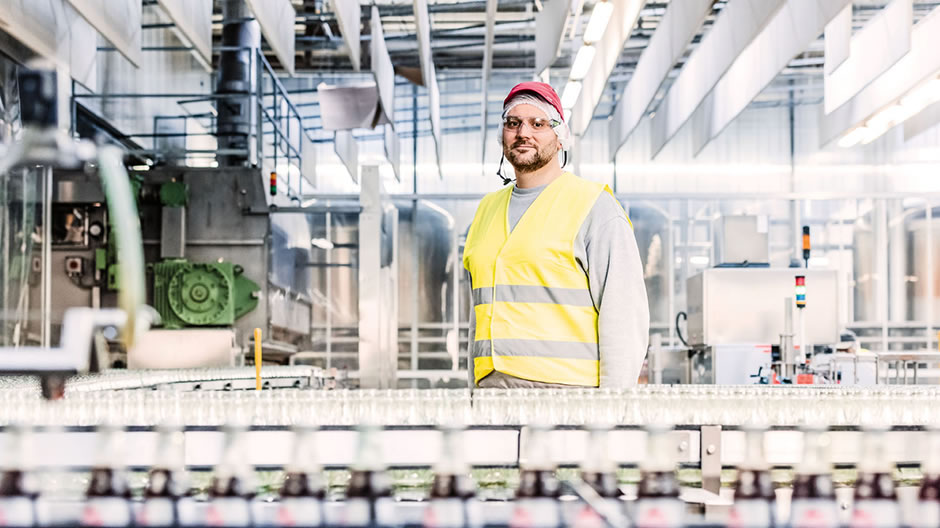
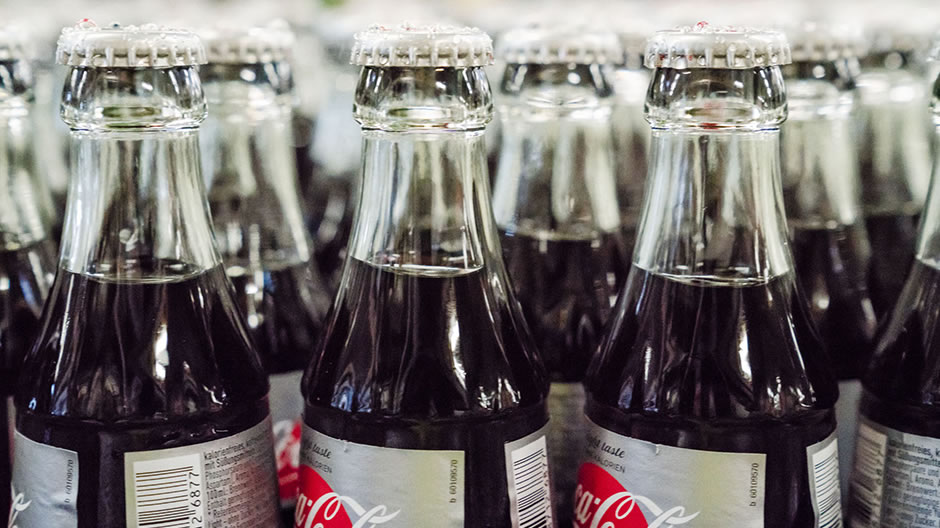
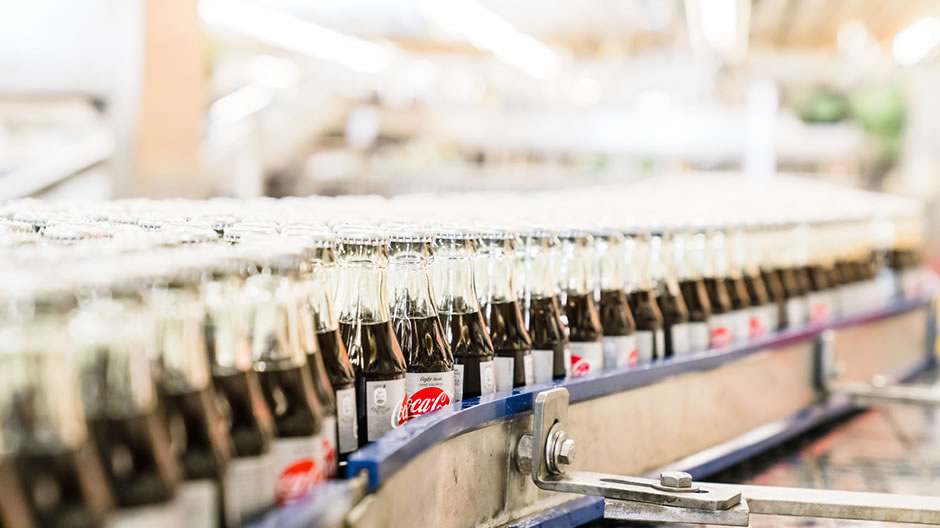
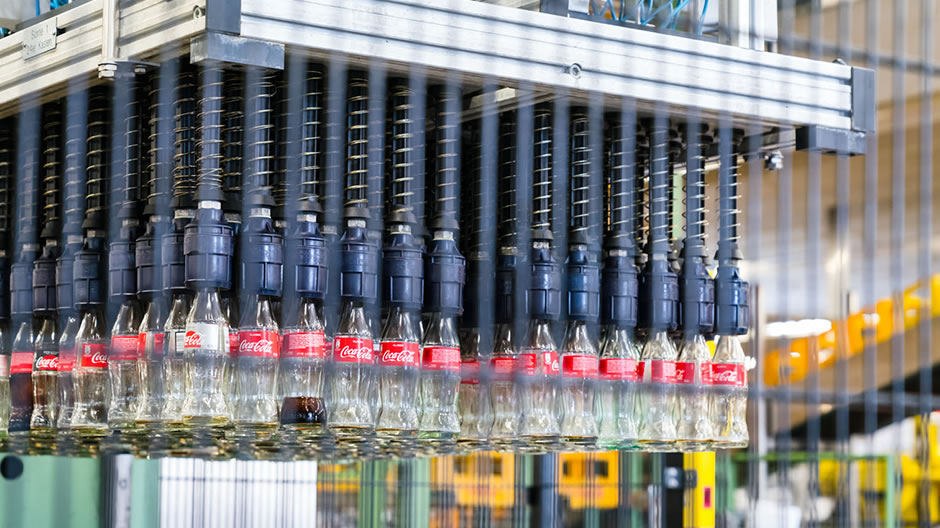

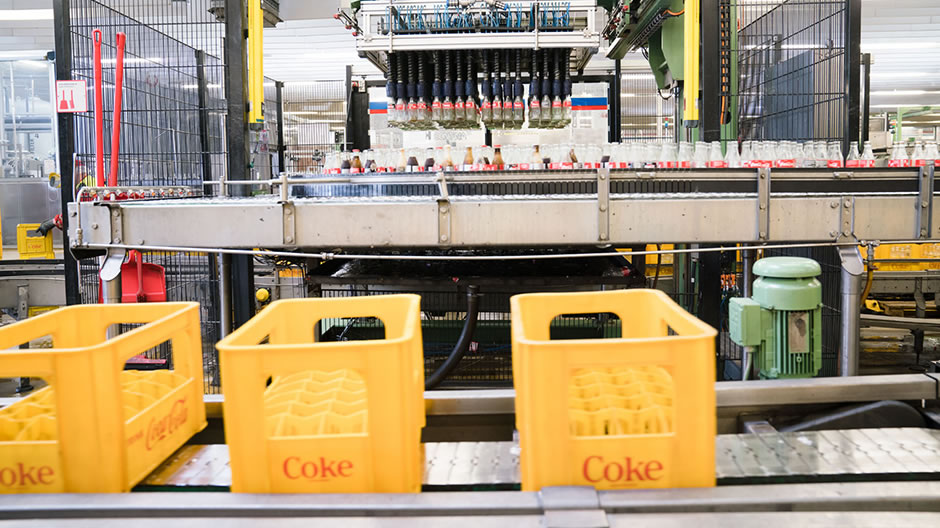
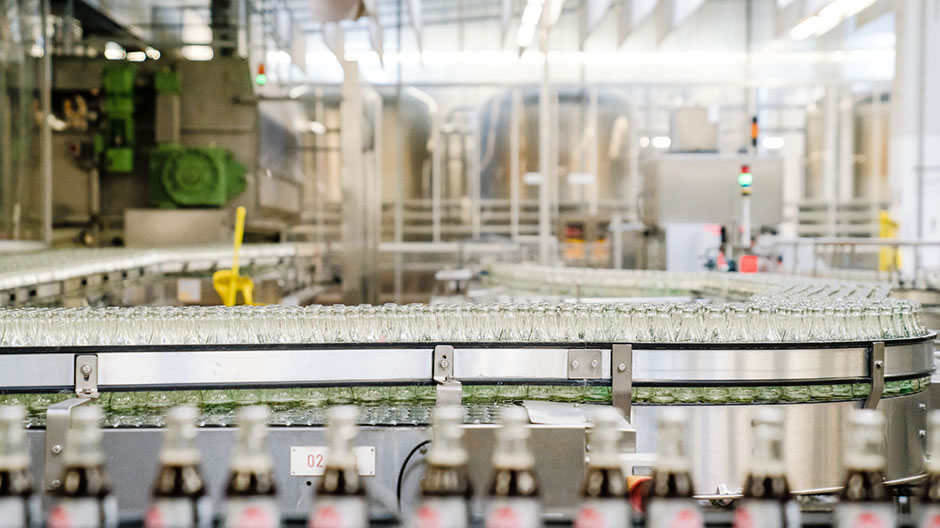
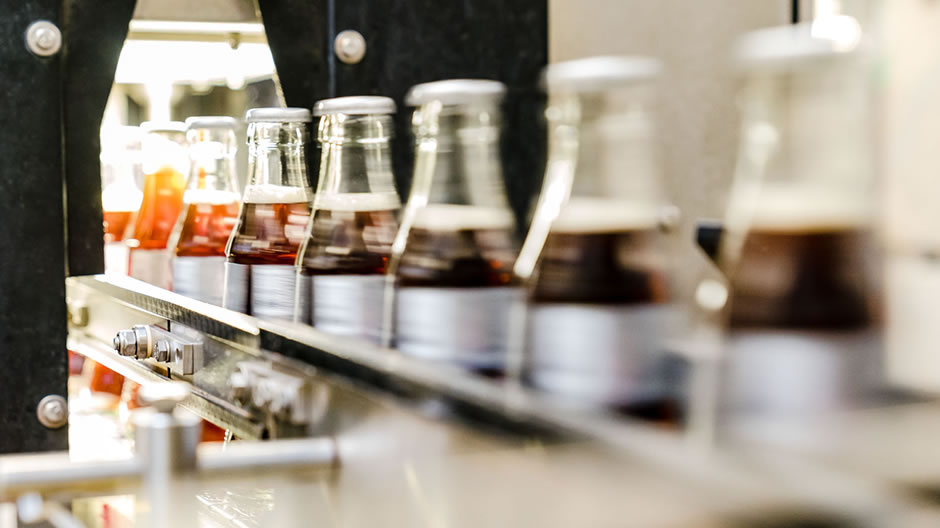
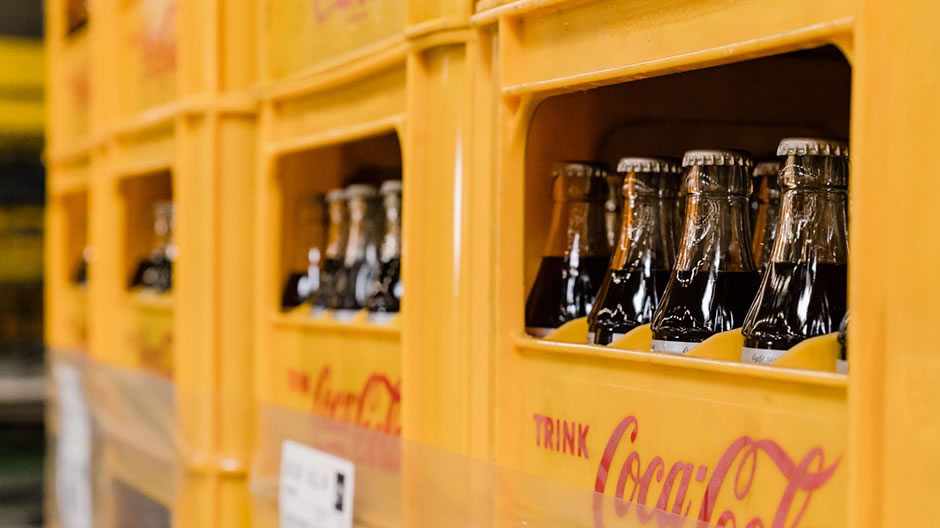
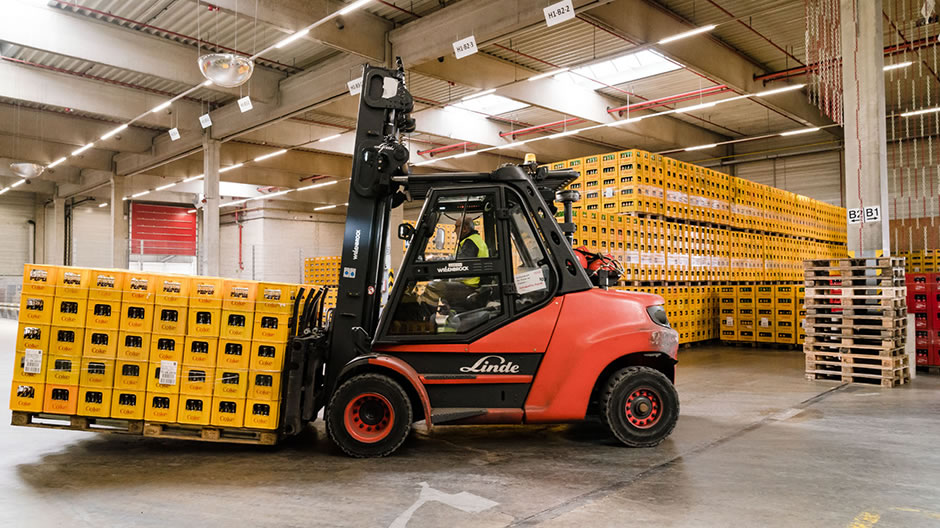
Da Achim alla regione in tutta sicurezza.
Dalle 11 ci si occupa degli ordini per il giorno successivo, senza nemmeno un foglio di carta, grazie alla gestione elettronica del deposito. I magazzinieri collaborano con dieci addetti alla preparazione degli ordini, per fare sì che i clienti ricevano, tra i circa 300 prodotti disponibili, esattamente ciò che hanno richiesto. Durante ogni turno un addetto movimenta fino a 18 tonnellate, equivalenti a circa due carichi di autocarro. I veicoli pronti vengono parcheggiati davanti all'edificio. Dalle 4 del mattino successivo, partiranno da qui i 17 autisti per eseguire le consegne nella regione.
Christian Walter, autista per le consegne, apre il telone del suo Antos 2540 rosso brillante. Quindi fa un segnale a Siegfried Schmülling, che guida un carrello elevatore. Si tratta di un cosiddetto elevatore triplo, cioè può spostare fino a tre pallet contemporaneamente. Così si raggiungono facilmente le tre tonnellate e mezza. La posizione di ciascun pallet nell'autocarro dipende dalle condizioni che si trovano presso il cliente: c'è una rampa? Quanto è grande la consegna? Il cliente ha un suo elevatore a forca o bisogna scaricare la merce con il piccolo transpallet che è sempre a bordo?
La clientela comprende grandi acquirenti come catene commerciali e attività di ristorazione, per esempio la mensa del porto di Bremerhaven. Ma si rifornisce anche il piccolo chiosco che ordina periodicamente una minima quantità di bottiglie da un litro. In un caso del genere, gli autisti a volte incassano ancora piccoli importi in contanti. È proprio questa varietà che piace al conducente Christian Walter: 28 anni, da quattro lavora alla Coca-Cola e da quasi due è un autista della «flotta rossa». Principalmente nel centro di Brema: sono 70 chilometri per ogni percorso, con molte fermate.
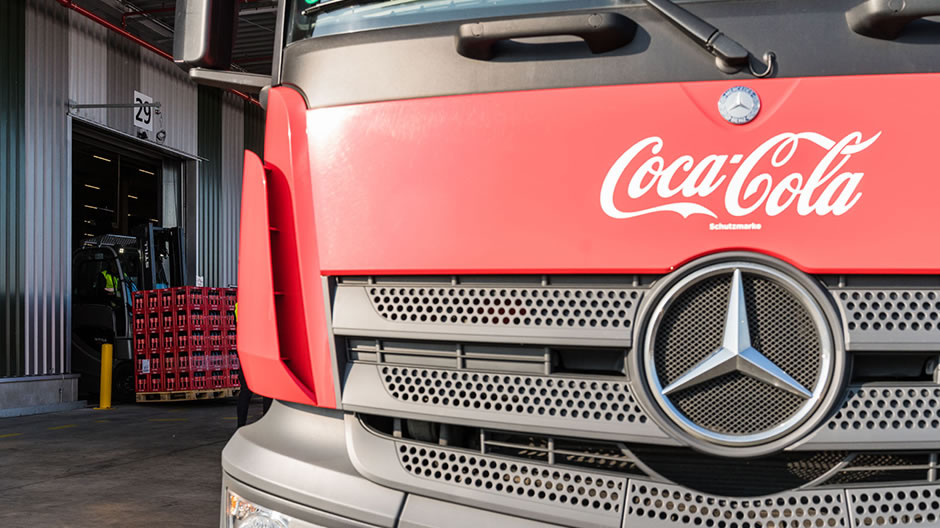
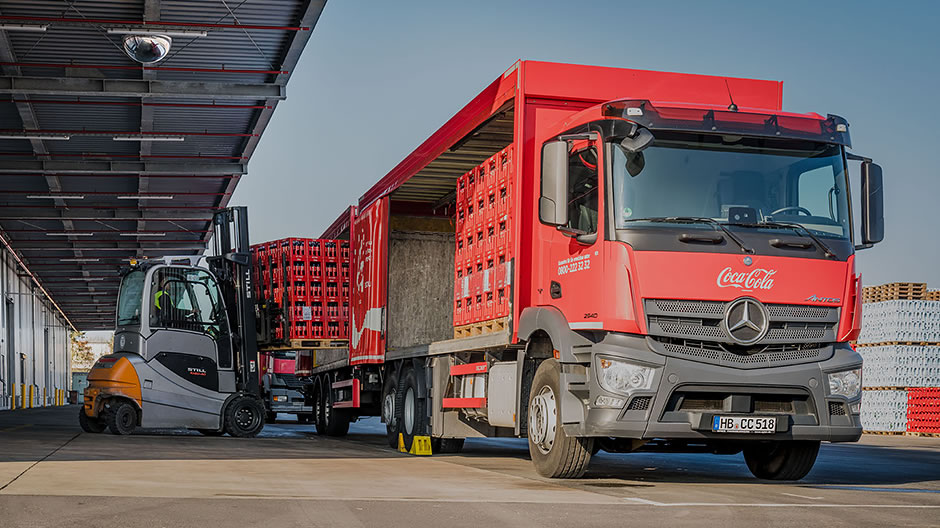

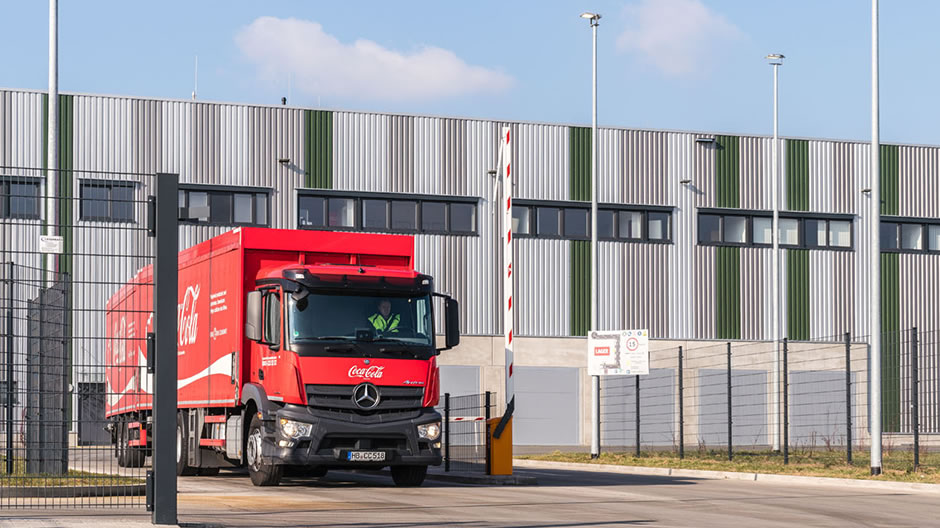
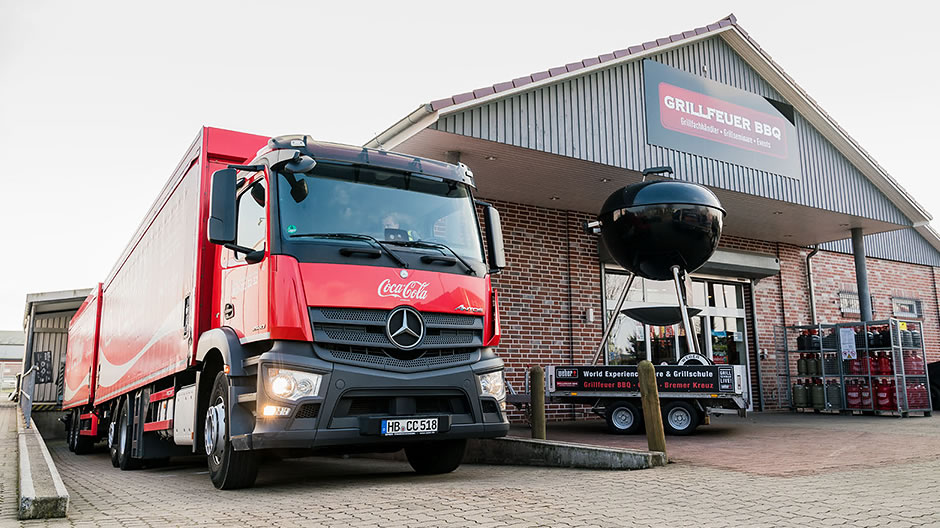
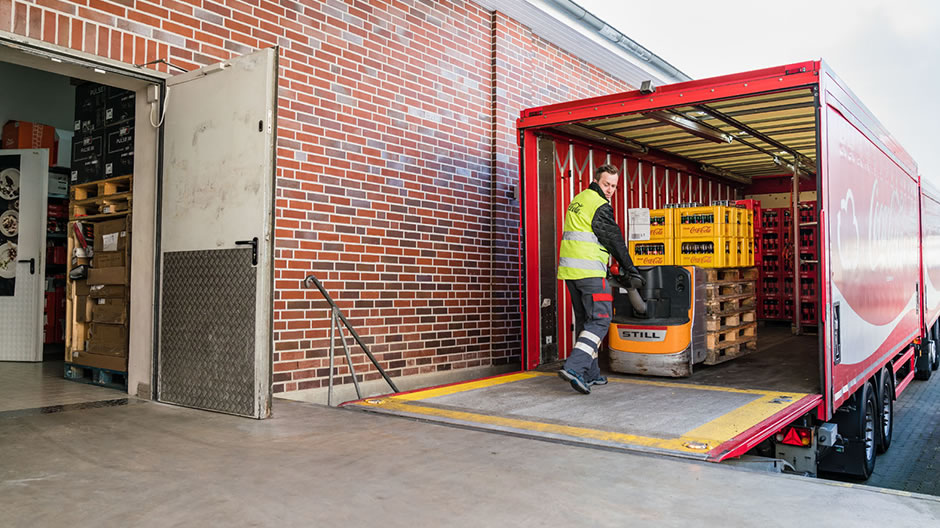
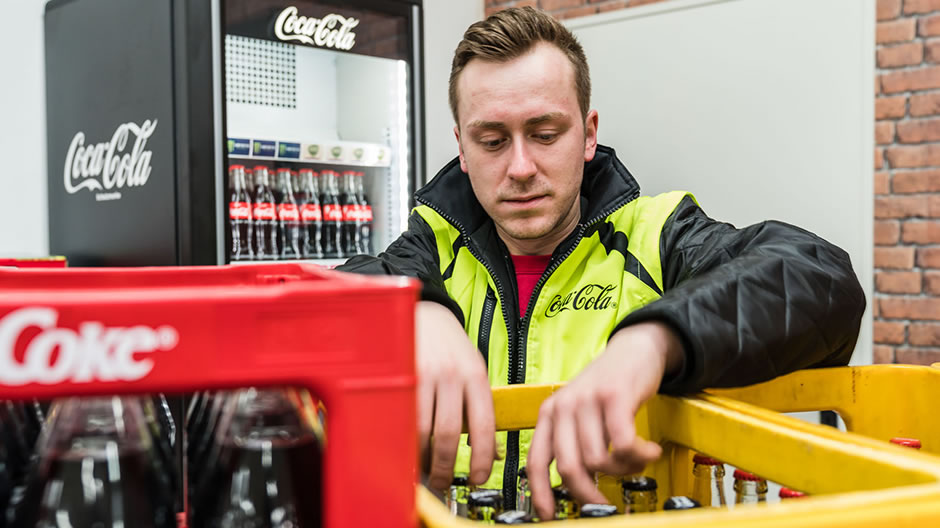
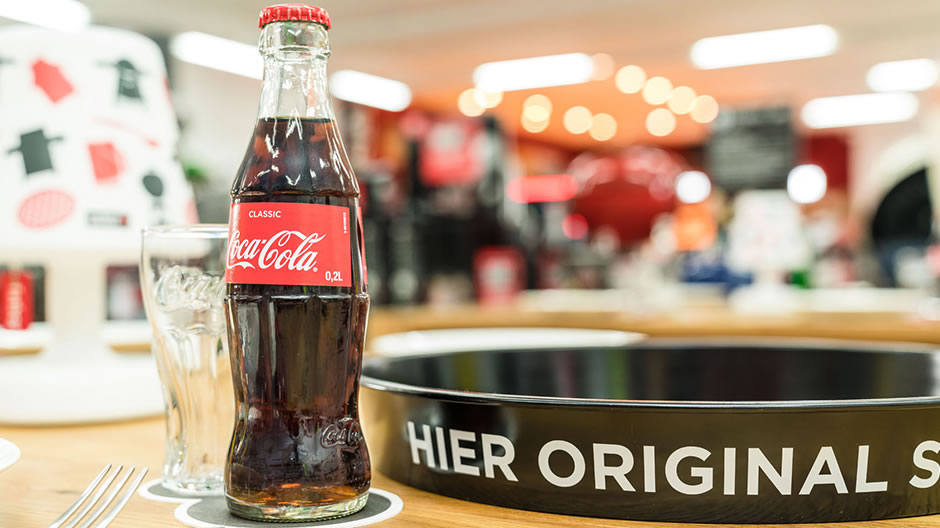
Ben attrezzati per l'alta stagione.
Il terreno ideale per il suo Antos, dotato di sistema antisbandamento e Active Brake Assist 3. A parte i sistemi di assistenza alla guida, quali equipaggiamenti sono irrinunciabili per lui? «Il riscaldamento del sedile e il climatizzatore», risponde Walter. Per lui è una sicurezza quando l'attività stagionale diventa molto intensa. E può fare freddo o caldo: i periodi con le maggiori vendite sono Pasqua e Natale, oltre naturalmente all'estate. Certo, anche in Germania del nord si accende la griglia e si mettono in fresco le bevande.
Oggi dodici casse gialle di bottiglie di Coca-Cola da 0,2 litri vanno a Grillfeuer BBQ. Questi appassionati del grill non solo vendono attrezzature di pregio per le grigliate, ma offrono anche corsi di cucina, barbecue e per l'appunto griglia. E qui non può mancare un vero classico: una Coca-Cola gelata in bottiglia di vetro.
Foto: Christian Schmid
Filmato: Martin Schneider-Lau
Commento
Effettua il login per aggiungere un commento.
6 commenti
Man lernt das der LKW Fahrer wenig fährt , aber viel arbeiten muss .
Eigentlich schade mit einem so schönen Antos .
Man lernt das der LKW Fahrer wenig fährt , aber viel arbeiten muss .
Eigentlich schade mit einem so schönen Antos .