
Getränkelogistik: Wie kommt die Coca-Cola in die Flasche und zum Verbraucher?
Wirtschaft & Logistik
Die Produktion bei Coca-Cola ist sicher, sauber und automatisiert. Auch bei der Auslieferung gelten hohe Standards. Deshalb setzt das Unternehmen nur auf schwere Verteiler-Lkw von Mercedes-Benz.
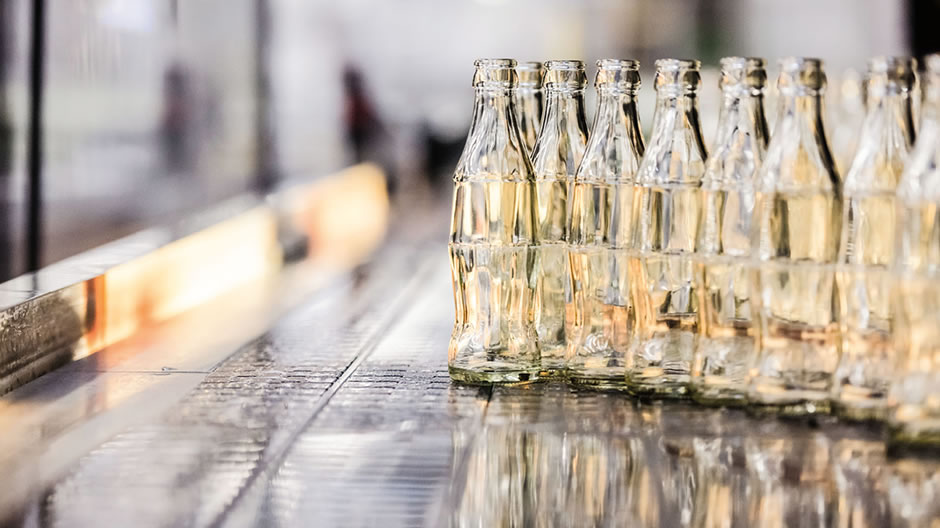
Blitzsauber. Retourniert, gereinigt, bereit für den nächsten Turnus: Bis zu 46.000 Flaschen werden in Hildesheim stündlich gefüllt.
Dieser Titel gehört auf den Soundtrack des Sommers: Das Öffnen der Kühlschranktür, das Geräusch von Glasflaschen, das Zischen des Kronkorkens. Eiskalte Coca-Cola aus der kleinen 0,2-Liter-Flasche ist Kult. „Mercedes-Benz Transport“ hat sich auf den Weg an die Quelle gemacht und die kleine Flasche auf ihrer Reise begleitet. Und die beginnt zum Beispiel in Hildesheim. Hier liegt einer der 16 Produktionsstandorte von Coca-Cola Deutschland. Die etwa 500 Mitarbeiter des Werkes sorgen dafür, dass rund um die Uhr volle Flaschen die fünf Produktionslinien verlassen. Das Ziel in diesem Jahr: Jeden Tag sollen eine Million Liter abgefüllt werden.
Die riesige Halle ist von Rauschen, Klackern und Klingeln erfüllt. Dieses Orchester dirigiert Alexander Haferkamp. Der 35-jährige Produktionsleiter muss alles im Blick haben: Werden genug leere Flaschen geliefert? Wie lang reicht der Sirup noch? Für welche Flaschengröße sollen die Anlagen gerade vorbereitet werden? Alle Maschinen werden beobachtet, Fehlfunktionen und Auffälligkeiten genau protokolliert. Mechaniker stehen ständig bereit, um die Ausfallzeiten zu minimieren. Für den studierten Braumeister und sein Team verläuft kein Tag wie der andere.
Genau abgestimmte Prozesse.
Für die kleine Colaflasche dagegen ist der Ablauf immer derselbe. Nach der Anlieferung werden Flaschen und Kästen getrennt, gereinigt und sortiert. Zwei Mitarbeiter sammeln andersförmige Flaschen vom Förderband. Im nächsten Schritt müssen etwaige Fremdkörper aus der Flasche entfernt werden. Dann geht es weiter zur Flaschen-Waschanlage. „Bei 80 Grad Celsius tauchen die Flaschen nacheinander in zwei verschiedene Laugen und werden dann mit klarem Wasser ausgespült. Danach ist die Flasche absolut sauber“, sagt Haferkamp. Anschließend ist der „Inspektor“ an der Reihe: Flasche für Flasche scannt das Gerät, dem keine noch so kleine Beschädigung entgeht.
Erst dann ist der entscheidende Moment gekommen: Im Füller gelangt die Coke in ihre Flasche. Zuvor wurde sie in einer Nebenhalle in unscheinbaren Tanks gemixt. Aus Trinkwasser, Sirup – die Rezeptur ist streng geheim – und natürlich Kohlensäure.
Zwischen 40.000 und 46.000 Flaschen schafft der Füller der Mehrweganlage pro Stunde. „Er ist das Herzstück der Produktionslinie und gibt den Takt vor: Die Leistung der anderen Produktionsgeräte ist auf die jeweilige Füllleistung abgestimmt“, sagt Produktionsleiter Haferkamp. Je nach Geschwindigkeit erhalten dann zum Beispiel elf Flaschen pro Sekunde ihre Etiketten und Kronkorken, bevor sie durch eine letzte Qualitätskontrolle gehen und in den sauberen gelben Kisten landen.
Dieser Artikel enthält zusätzliches Informationsmaterial (Videos, Bilder und Berichterstattung etc.) für registrierte Mitglieder. Um den Artikel vollständig zu erleben, logge dich bitte mit deinem RoadStars-Account ein oder registriere dich kostenlos.
Werde ein RoadStar und erhalte Zugang zu exklusiven Inhalten und Aktionen!
Login für RoadStars-Mitglieder
Noch kein Mitglied? Jetzt RoadStars beitreten
Erhalte einen exklusiven Zugang zu aufregenden Events und Aktivitäten, die nur RoadStars bieten kann.
RoadStars beitreten„Der Kunde erwartet die richtige Ware, in der richtigen Menge, zum richtigen Zeitpunkt und in der richtigen Qualität. Deswegen ist eine gut funktionierende Auslieferungslogistik extrem wichtig.“
– Francis Driessen, Netzwerk-Logistikleiterin für die Standorte Achim und Lüneburg
In Gruppen von 40 Kisten verlässt die Coca-Cola nun die Produktionshalle. Etwa eine Stunde lang ist eine Flasche auf den Hildesheimer Förderbändern unterwegs gewesen. Von der Palettierungsanlage geht es ins Lager und von dort direkt an Kunden sowie in die Distributionszentren der Region.
„124 Tage ohne Arbeitsunfall. Längste Zeit ohne Arbeitsunfall: 370 Tage.“ Die Tafel am Eingang des Auslieferungslagers in Achim bei Bremen zeigt: Bei Coca-Cola Deutschland nimmt man Sicherheit ernst. Kein Wunder also, dass Lkw von Mercedes-Benz den größten Teil der 17 Fahrzeuge starken Flotte ausmachen. „Der Kunde erwartet die richtige Ware, in der richtigen Menge, zum richtigen Zeitpunkt und in der richtigen Qualität. Deswegen ist eine gut funktionierende Auslieferungslogistik extrem wichtig“, sagt Francis Driessen, Netzwerk-Logistikleiterin für die Standorte Achim und Lüneburg. Der Blick in die 2017 bezogene Lagerhalle bestätigt dies. Alles wird penibel sauber und ordentlich gehalten. Geht doch einmal etwas zu Bruch, sind die Scherben ruckzuck verschwunden.
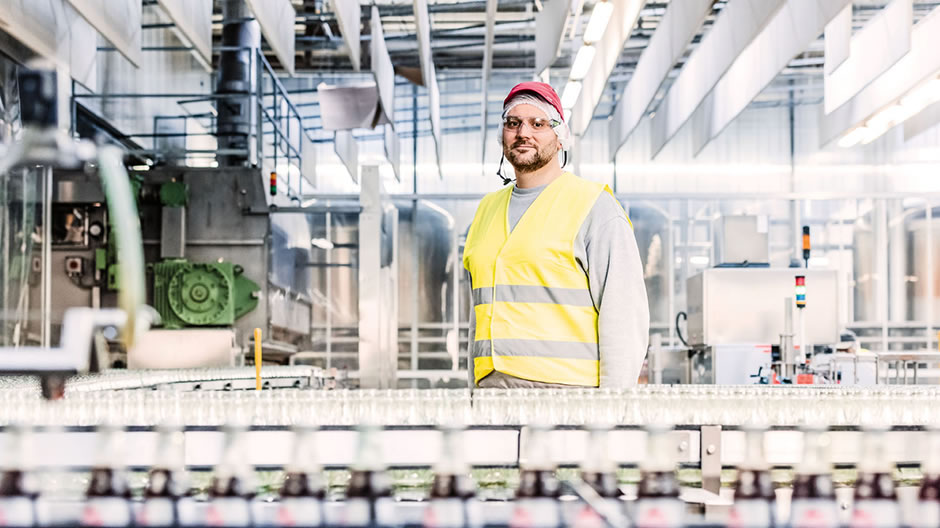
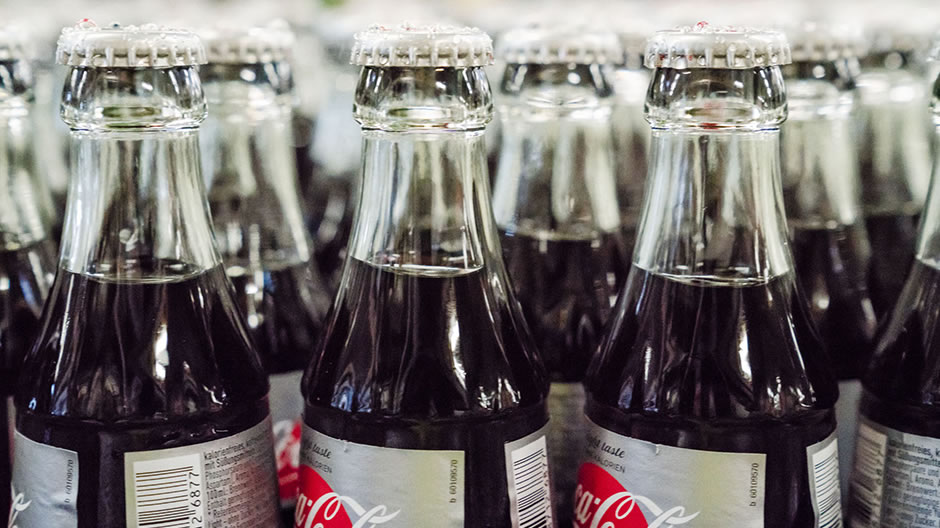
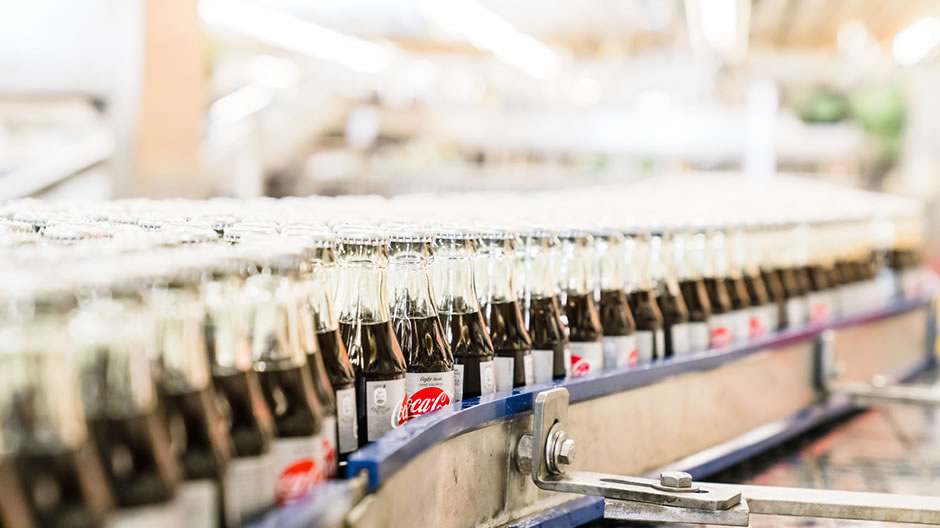
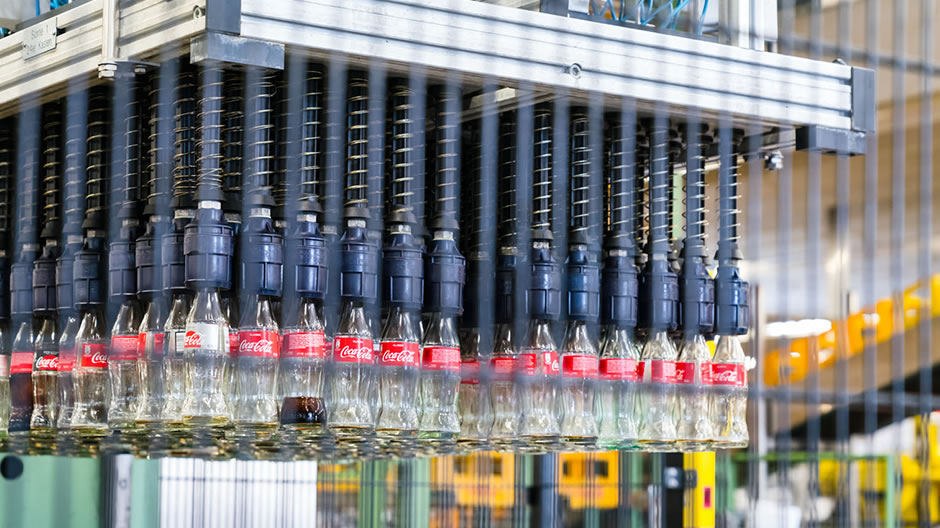

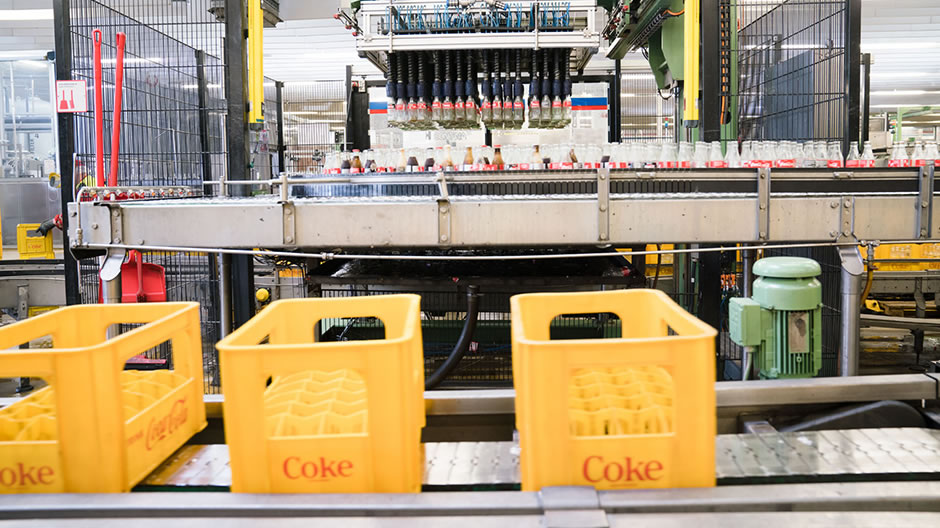
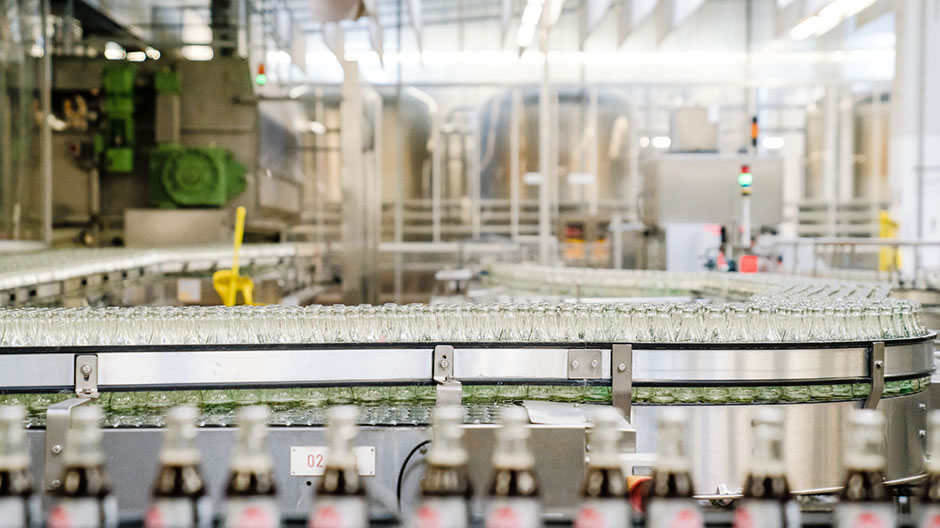
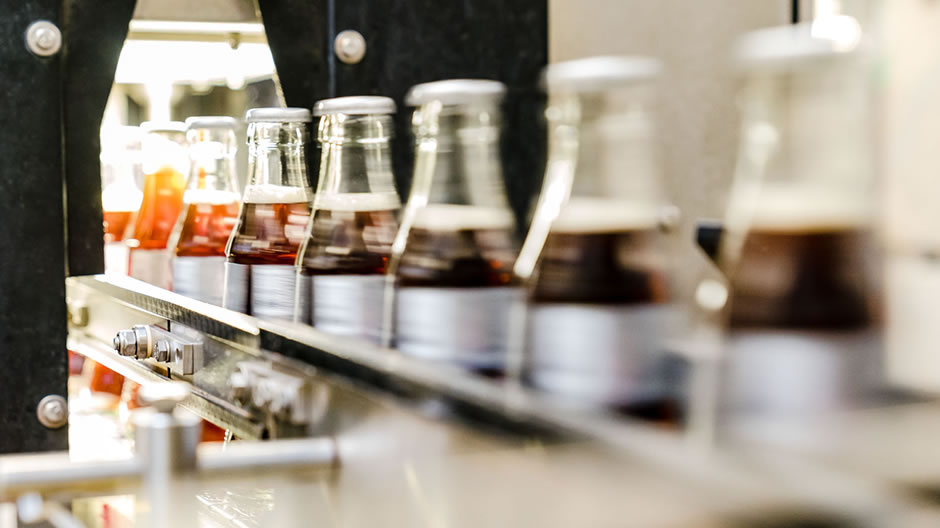
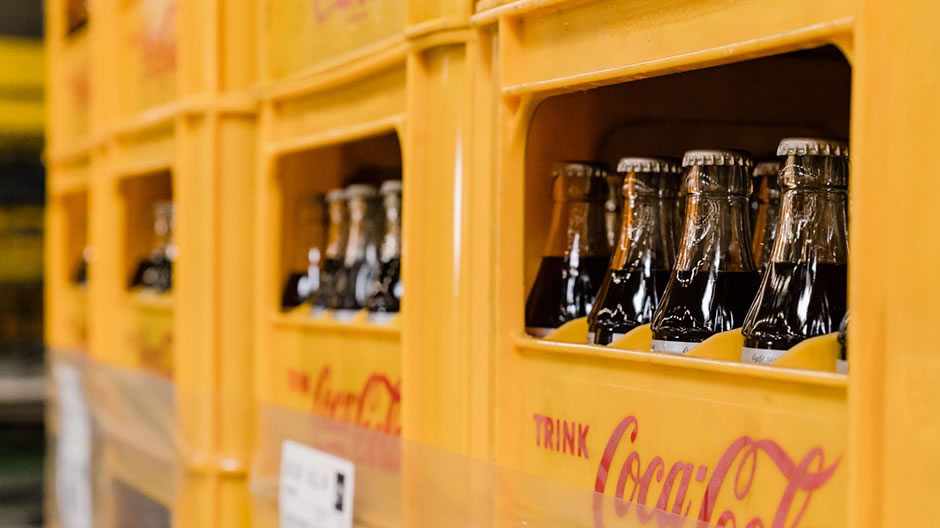
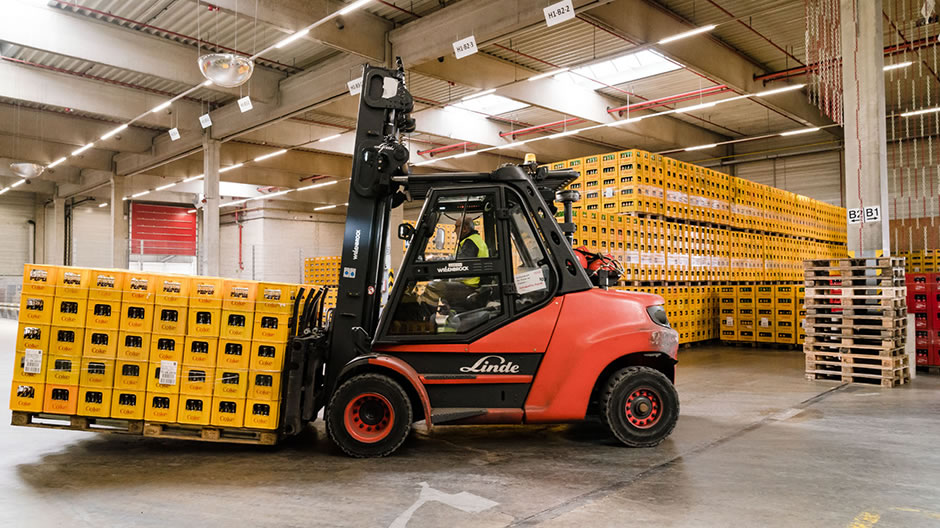
Zuverlässig von Achim aus in die Region.
Ab 11 Uhr werden die Aufträge für den folgenden Tag zusammengestellt, komplett papierlos dank der elektronischen Lagerplatzverwaltung. Mit zehn Kommissionierern sind die Lagermitarbeiter unterwegs, damit die Kunden aus den rund 300 Produkten exakt die gewünschten geliefert bekommen. Bis zu 18 Tonnen bewegt ein Arbeiter in jeder Schicht, das entspricht etwa zwei Lkw-Ladungen. Abgefertigte Fahrzeuge werden vor dem Gebäude geparkt. Von dort starten die 17 Auslieferungsfahrer am nächsten Morgen ab 4 Uhr früh in die Region.
Auslieferungsfahrer Christian Walter öffnet die Schiebeplane seines leuchtend roten Antos 2540. Dann gibt er Staplerfahrer Siegfried Schmülling ein Zeichen. Der steuert einen sogenannten Dreifachstapler. Bis zu drei Paletten kann dieser gleichzeitig bewegen. Da kommen schnell dreieinhalb Tonnen Gewicht zusammen. Welche Palette welche Position im Lkw erhält, hängt von den Bedingungen vor Ort beim Kunden ab: Gibt es eine Rampe? Wie groß ist die Lieferung? Hat der Abnehmer einen eigenen Gabelstapler oder wird mit dem kleinen Hubwagen abgeladen, der immer mit an Bord ist?
Zum Kundenstamm gehören Großabnehmer wie Handelsketten und Gastronomiebetriebe wie beispielsweise die Hafenkantine in Bremerhaven. Aber auch der kleine Kiosk, der regelmäßig die Mindestmenge Literflaschen bestellt, wird beliefert. In so einem Fall kassieren die Fahrer manchmal noch Kleinbeträge in bar. Für Fahrer Christian Walter ist es genau diese Bandbreite, die ihm Spaß macht. Seit vier Jahren arbeitet der 28-Jährige bei Coca-Cola, seit knapp zwei Jahren ist er als Fahrer in der „roten Flotte“ unterwegs. Hauptsächlich in der Bremer Innenstadt – das sind pro Tour 70 Kilometer mit vielen Stopps.
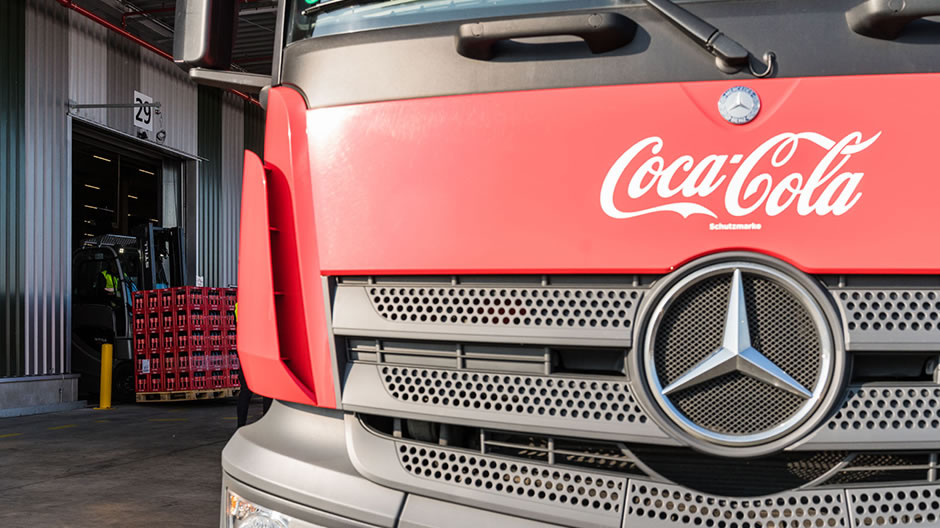
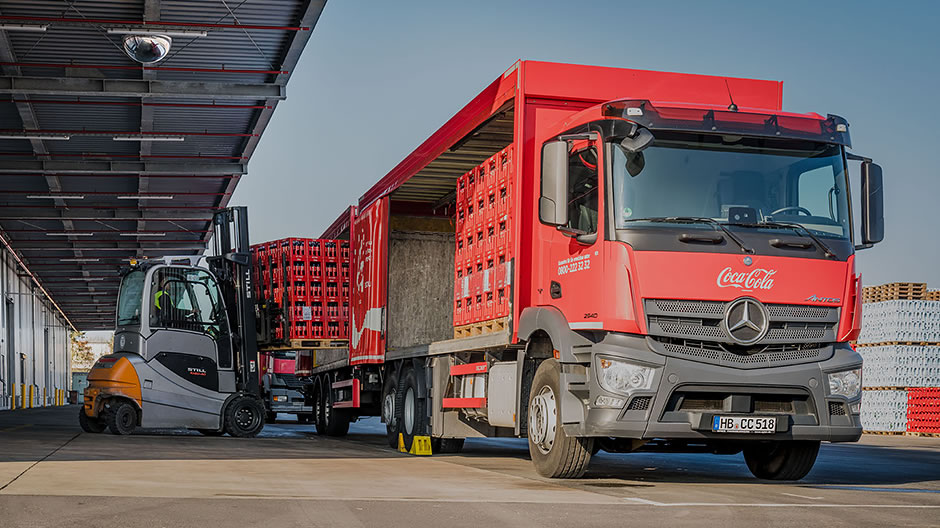

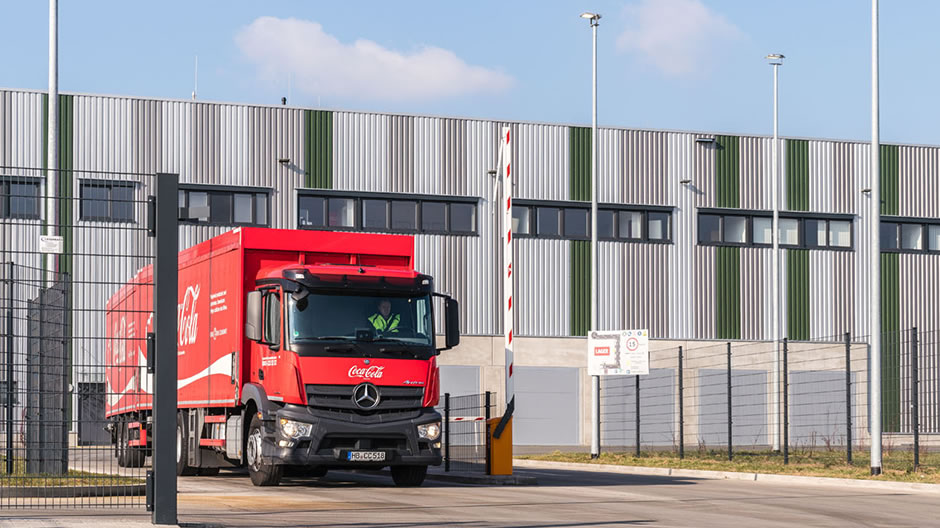
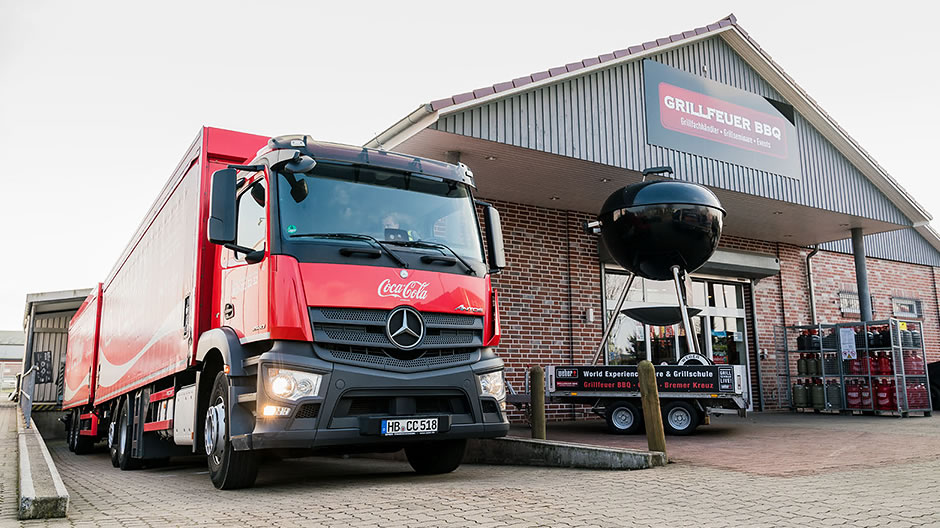
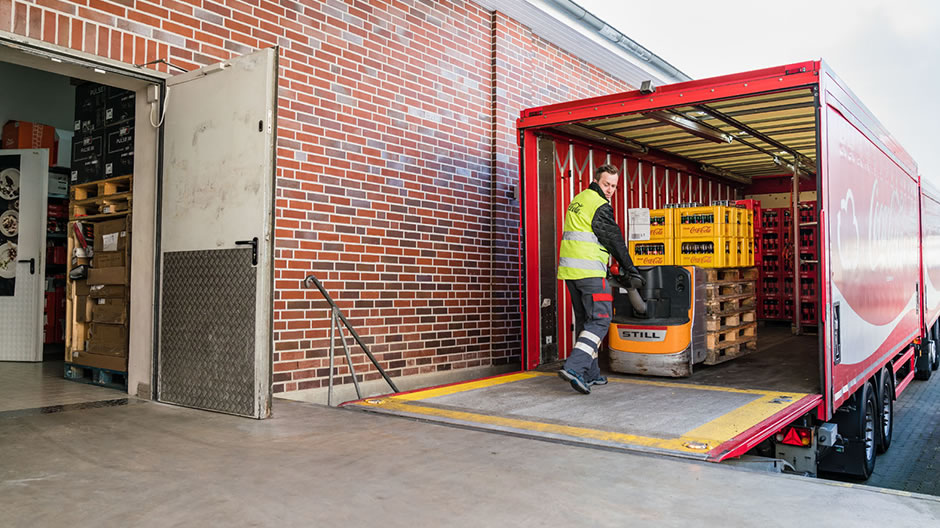
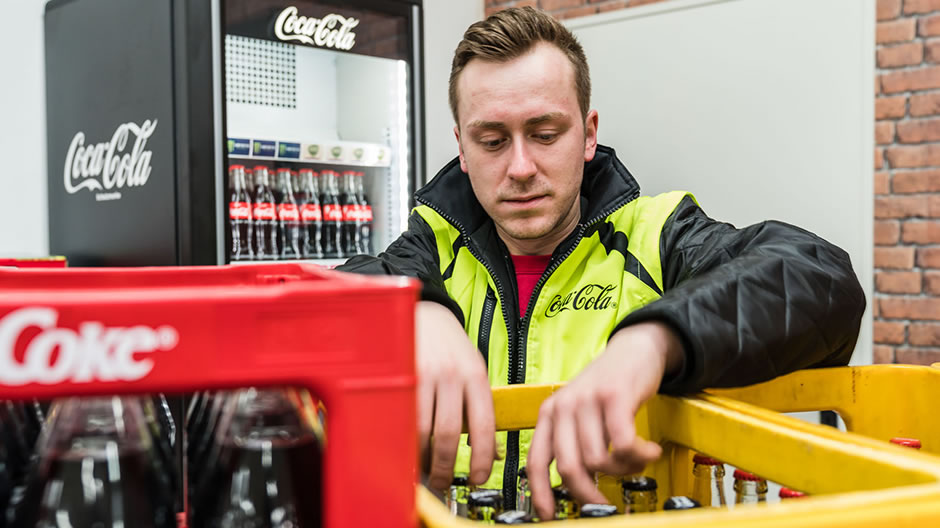
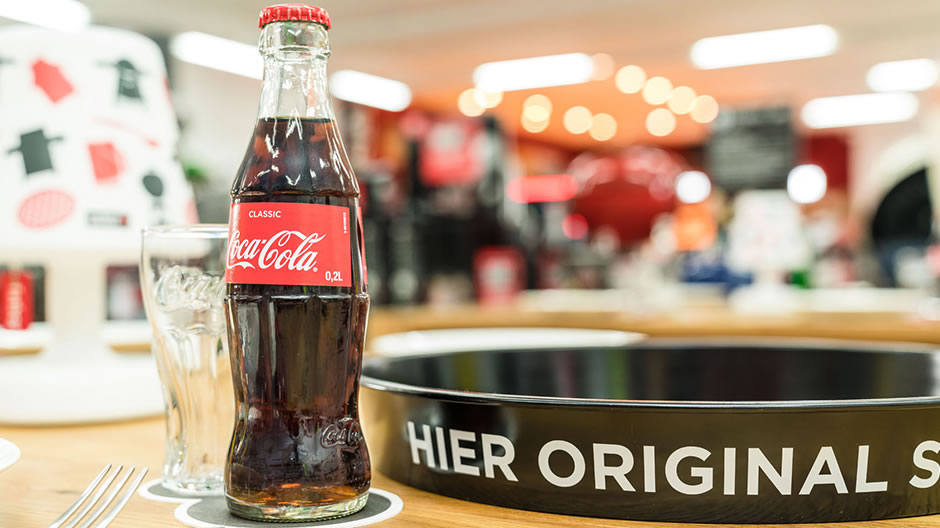
Gut gerüstet für die Hochsaison.
Ein ideales Terrain für seinen Antos mit Spurhalte-Assistent und Active Brake Assist 3 an Bord. Auf welche Ausstattungen er außer den Assistenzsystemen nicht verzichten möchte? „Sitzheizung und Klimaanlage“, sagt Walter. Auf die kann er zählen, wenn es im Saisongeschäft besonders viel zu tun gibt. Und dann ist es entweder heiß oder kalt: Ostern und Weihnachten sind die umsatzstärksten Zeiten. Und natürlich der Sommer. Klar, dann werden auch in Norddeutschland die Grills angefeuert und die Getränke kaltgestellt.
Zwölf gelbe Kisten mit 0,2-Liter-Flaschen Coca-Cola gehen heute an Grillfeuer BBQ. Die Grill-Enthusiasten verkaufen nicht nur hochwertige Grills, sondern bieten auch Koch-, BBQ- und Grillkurse an. Und dazu passt dann einfach der Klassiker am besten: eiskalte Coca-Cola aus der Glasflasche.
Fotos: Christian Schmid
Film: Martin Schneider-Lau
Kommentar
Logge dich bitte ein, um einen Kommentar hinzuzufügen.
6 Kommentare
Man lernt das der LKW Fahrer wenig fährt , aber viel arbeiten muss .
Eigentlich schade mit einem so schönen Antos .
Man lernt das der LKW Fahrer wenig fährt , aber viel arbeiten muss .
Eigentlich schade mit einem so schönen Antos .