
Distribution transport: Rohr Spezialfahrzeuge offers through-loading solution based on the Actros
Vehicle & technology
The application information centre (BIC) offers optimal solutions for all areas of transport. Christian Gietl, expert in refrigerated bodies at Rohr Spezialfahrzeuge, on the capability of a through-loadable road train in combination with the new Actros.
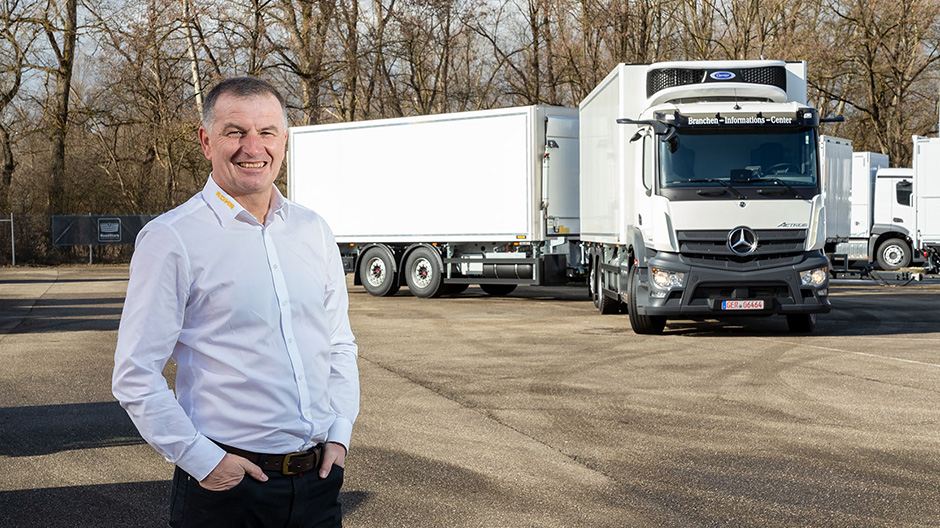
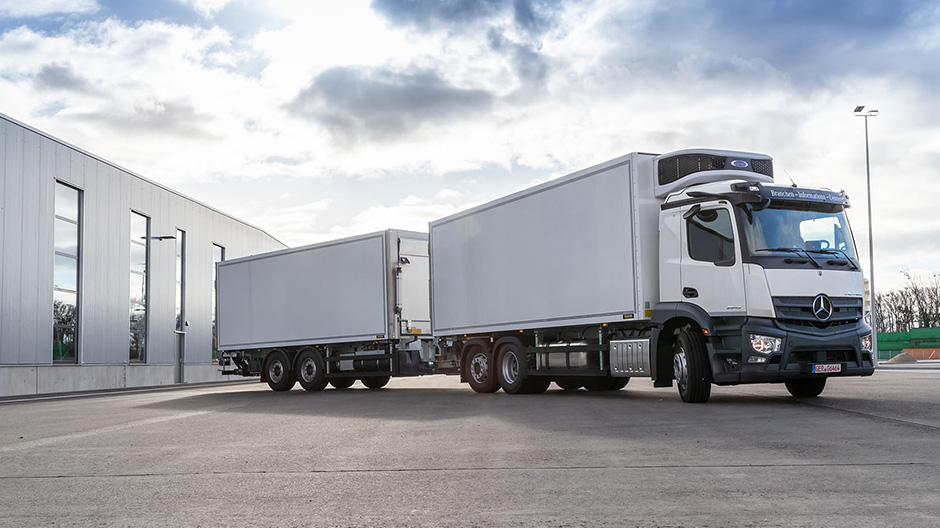
Rohr Spezialfahrzeuge GmbH is looking to make processes in food logistics more efficient. This is also how the new generation of the DLE 31-A through-loading system was created based on a new Actros 2543. The safety and assistance systems in the Actros are of particular help in distribution transport. When manoeuvring, for example, MirrorCam gives the driver valuable support. The same applies to turning. Here, Sideguard Assist can warn of moving and stationary objects in the monitoring zone to the right of the truck if there is any danger of collision.
This article contains additional material (videos, images and reports etc.) for registered RoadStars members. In order to experience the article to the full, you need to log in with your RoadStars account or register for one free of charge.
Become a RoadStar and gain access to exclusive content and campaigns!
Login for RoadStars members
Not yet a member? Join RoadStars now
Obtain exclusive access to exciting events and activities which only RoadStars can offer.
Join RoadStarsThe main component of the new trailer is the front cover in combination with a retractable drawbar. The body of the Actros has a tail lift, which can be used to transport goods from one of the two load carriers to the other.
The combination can hold two sets of 18 Euro pallets or two sets of 30 roller containers. The drawbar between the motor vehicle and the trailer is extended as soon as the vehicle has docked at the loading ramp.
This creates the space required by the lowered tail lift or the bridge between the two load containers.
Since the operating system is accessible from the outside, the driver does not have to switch between the motor vehicle, trailer and external area. There is no longer any need for time-consuming uncoupling, and only one docking point is used at the distribution centre or market. The vehicle is ready for loading or unloading in less than three minutes.
Significant time savings on the whole. The system was optimised via remote control of the tail lift from the trailer. It allows the driver to close the front container once it has been loaded without having to leave the loading area.
________________________
Test drive in Wörth: over 180 fully constructed vehicles are on hand for examining and testing at the application information centre (BIC) in Wörth. Skilled experts explain everything there is to know about the topic of interest and show visitors around.
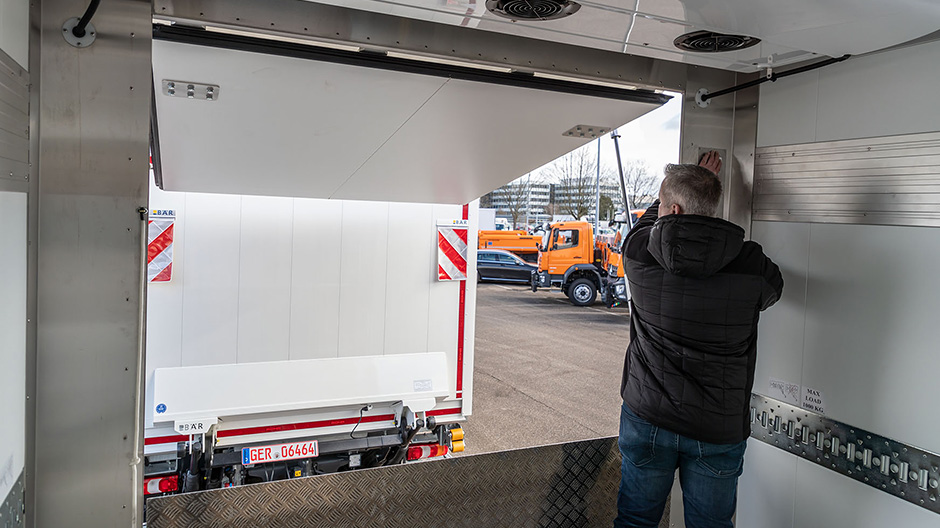
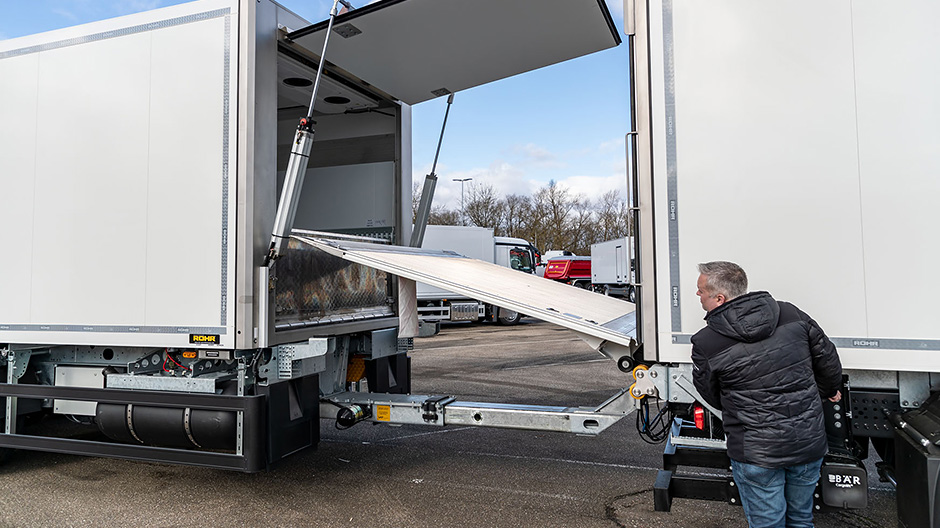
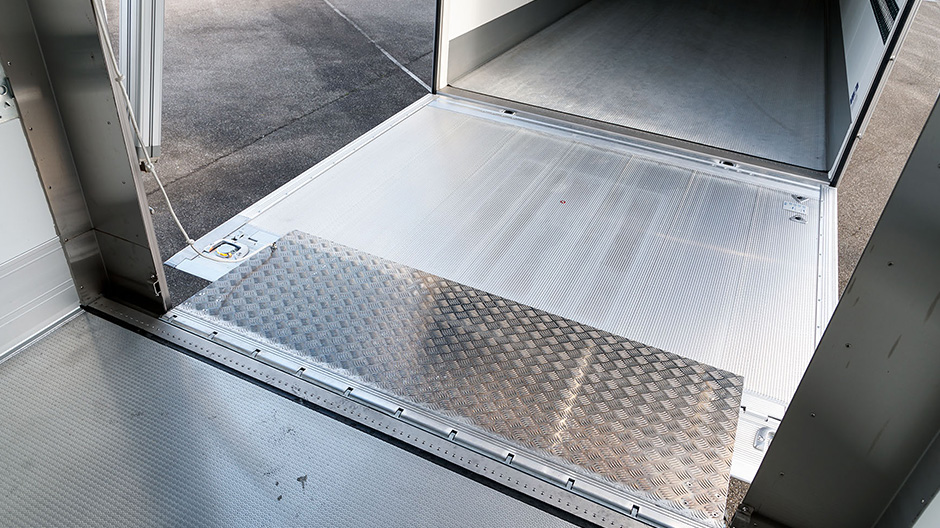
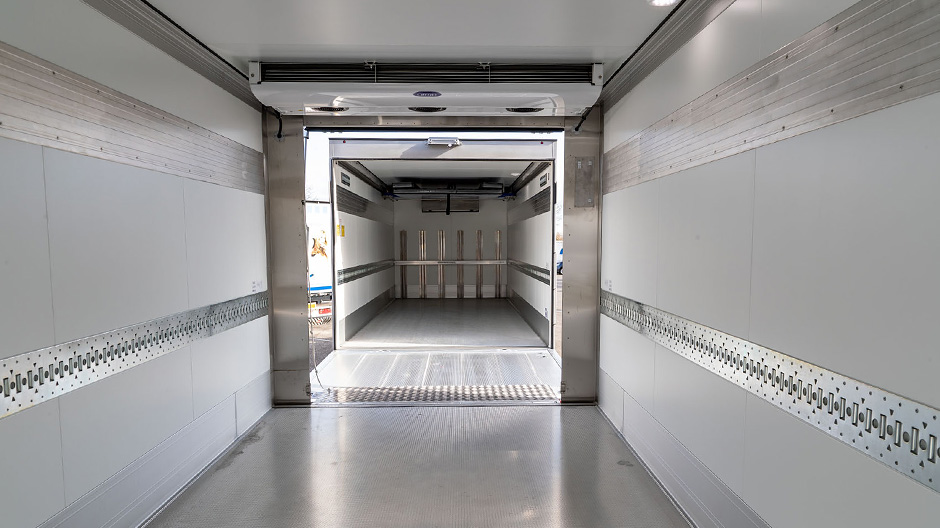
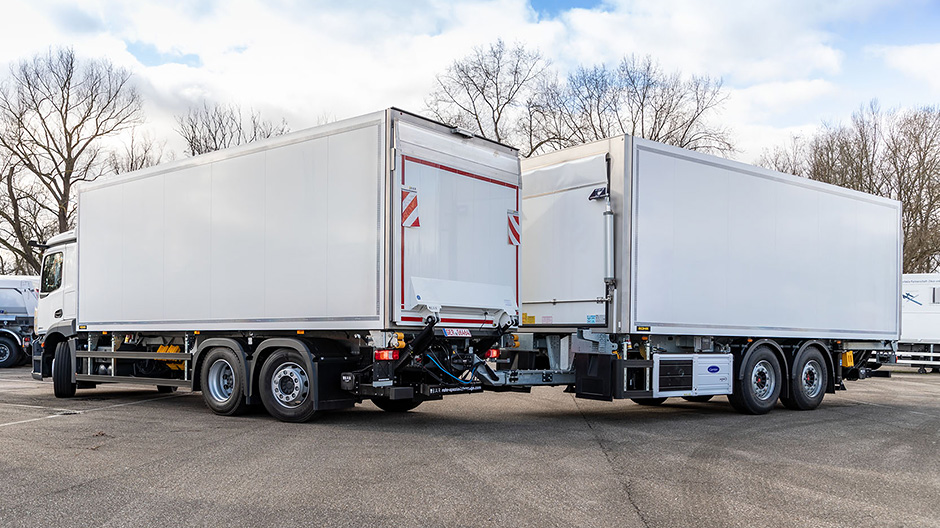
Photos and video: Henrik Morlock
Comment
Please log in to post a comment.
12 comments
Schöner Artikel und schöne Fotos und ein tolles Video.
Grüße Jörg 👍👍👍👍👍⛟😎😷
Schöner Artikel und schöne Fotos und ein tolles Video.
Grüße Jörg 👍👍👍👍👍⛟😎😷
Ich bin äußerst überrascht komme aus dem Bereich abrollcontainer und zuletzt Air Cargo man lernt ja niemals aus.
Ich bin äußerst überrascht komme aus dem Bereich abrollcontainer und zuletzt Air Cargo man lernt ja niemals aus.