
At Baam in Karlsruhe the staff rely on Mercedes-Benz Uptime
Service
Fresh foods specialist Baam must adhere precisely to the time schedule stipulated by its customers. The company can’t afford any unplanned visits to the workshop. With the help of Mercedes-Benz Uptime, the haulage company is now able to intervene before a tour goes wrong.
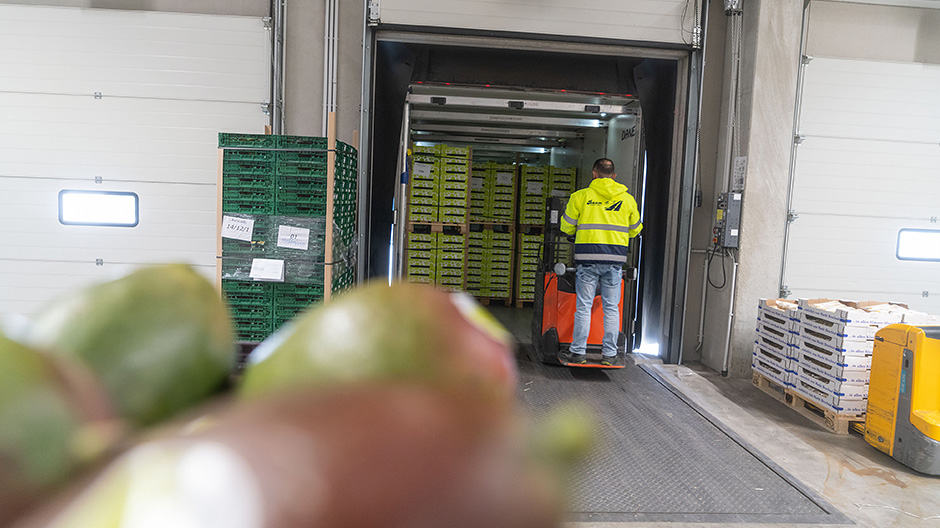
A promise to provide fresh goods on a daily basis. Baam specialises in transporting fruit and vegetables.
Fresh fruit and vegetables every day – today this is what is expected of any western European supermarket. However, in order for the consumer to find a large selection of good quality products in the fruit and vegetable section every day whatever the season, fresh food transportation specialists must be masters of their trade.
One of these experts is Baam Transporte und Lagerung from Karlsruhe in Germany. The company does serve other customers, but over the last 25 years Managing Director, Andreas Baam, has become a specialist for the transportation of fresh foodstuffs such as fruit and vegetables, dairy products, meat and delicatessen products. The logistics service provider also transports and stores frozen goods and temperature-sensitive pharmaceutical products. Just over a hundred trucks, most of which are Actros, and three warehouse facilities in the Karlsruhe region are available to Baam customers.
“Our continuous growth is due primarily to customers from the foodstuffs industry,” says Andreas Baam. There are, for example, smaller to medium-sized producers who have fruit orchards at Lake Constance or in the "Altes Land" region on the Elbe, near Hamburg. Customers also include international companies such as SanLucar that produce fruit and vegetables all over the world and ship them to Germany. “We try to bundle the produce of different contractors and then deliver them,” Baam explains. Destinations are then, for example, the regional central warehouses of large supermarket chains like Aldi Süd or Edeka which transport the goods “the last mile” to their shops themselves.
Almost no one knows this segment and the logistics required better than Andreas Baam. The 59-year old took over his grandfather's Karlsruhe-based company when he was only 21. In 1995 he built a modern transportation centre here. That was the point when growth really began and the company truly took off.
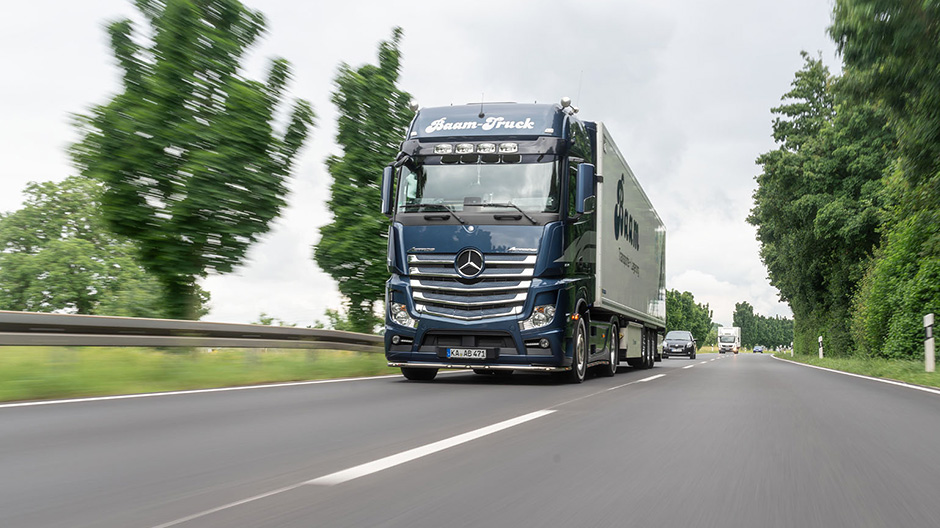
Always on target thanks to Mercedes‑Benz Uptime.
“For customers from the foodstuffs industry, absolute punctuality for deliveries is crucial,” Baam tells us. “Even if we are only an hour too late, it is possible that the customer may refuse to accept the goods.” The retailer's truck for the next leg of the journey has then perhaps already left and fresh fruit and vegetables have already been ordered for the next day. The result: Baam is left with the load and at best can only sell them off at low prices at the wholesalers. “This is very annoying, but rarely happens to us. If it did, we wouldn't get any more orders.”
In addition to good planning, responsible staff in the offices, in the warehouse and behind the wheel, the reliability of the trucks is also an important factor for success in the business of transporting foodstuffs. Here, Baam relies on Mercedes‑Benz Trucks and the related services. For some time now the company has been successfully using Mercedes‑Benz Uptime, an additional service which is part of the Mercedes‑Benz Service contracts.
“Our continuous growth is due primarily to customers from the foodstuffs industry.”
– Andreas Baam, Managing Director
Monitoring the technical condition of trucks.
With the help of a fully automatic telediagnosis, Mercedes‑Benz Uptime continuously checks the status of vehicle systems in the truck in real-time. The data is interpreted, critical states identified and recommended action given. Where necessary, the customer is even immediately provided with a specifically tailored solution which has been optimally coordinated with the respective route planning and vehicle status. The aim is to have the trucks out on the road for as long as possible and to have all transport orders reliably completed. “Thanks to Mercedes‑Benz Uptime our fleet has become even more reliable,” reports Manuel Morte, Fleet Manager at Baam. Since the system was introduced, break-down vehicles and unplanned visits to the workshop have been effectively reduced.
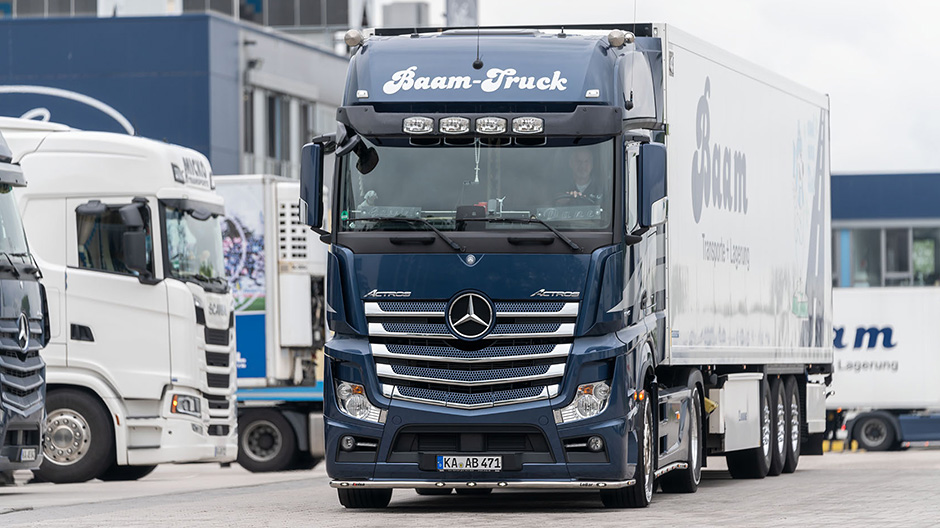
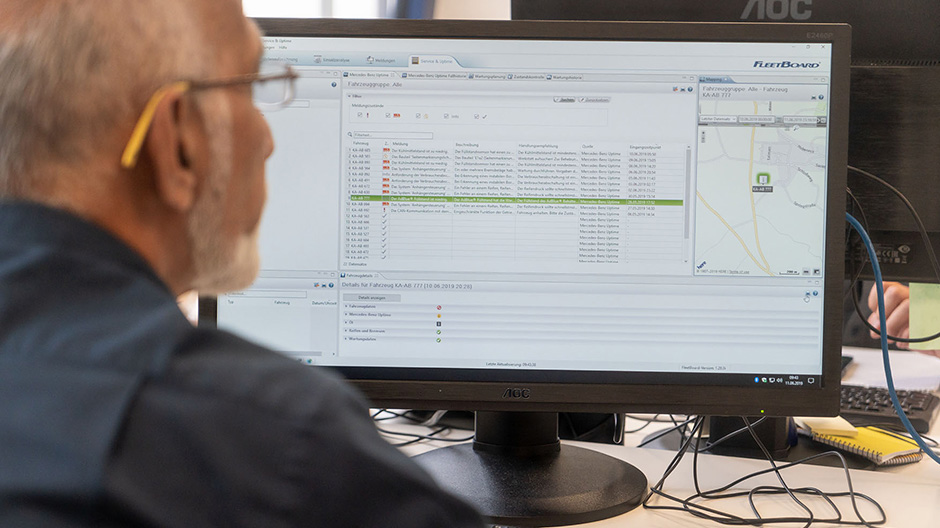
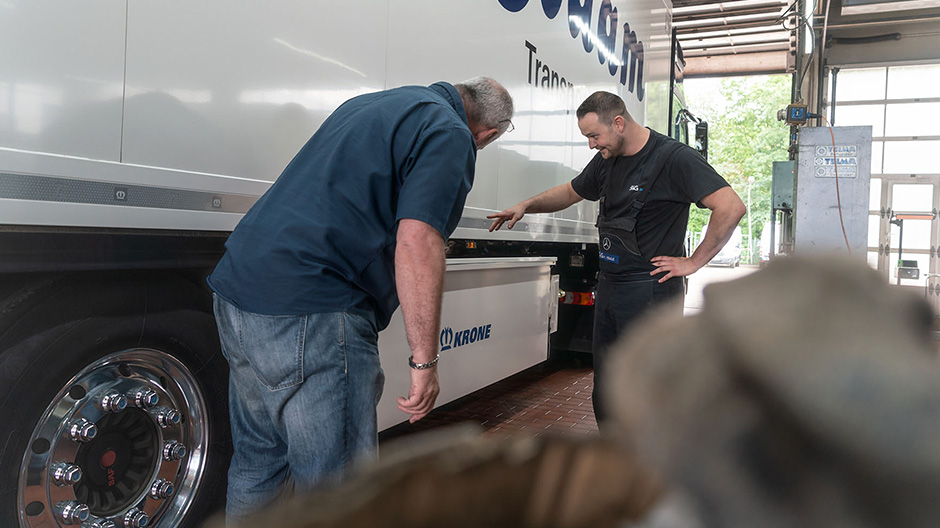
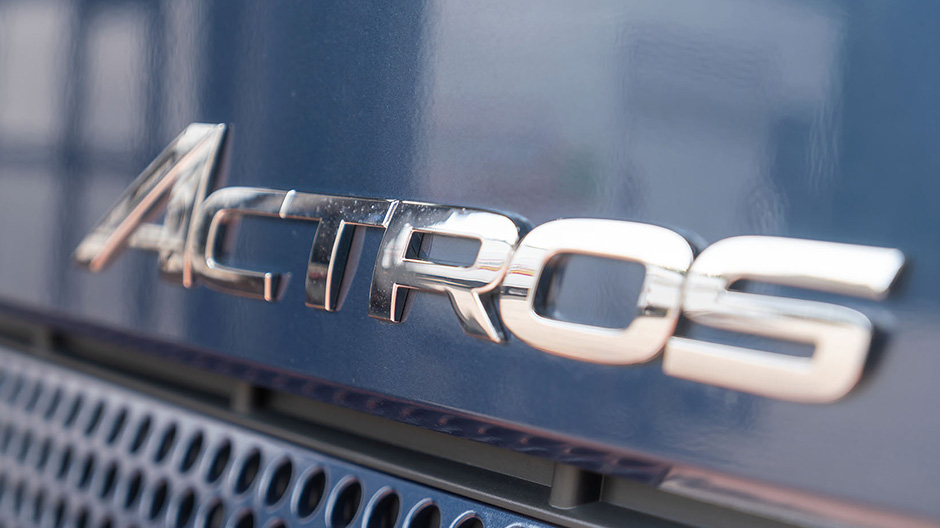
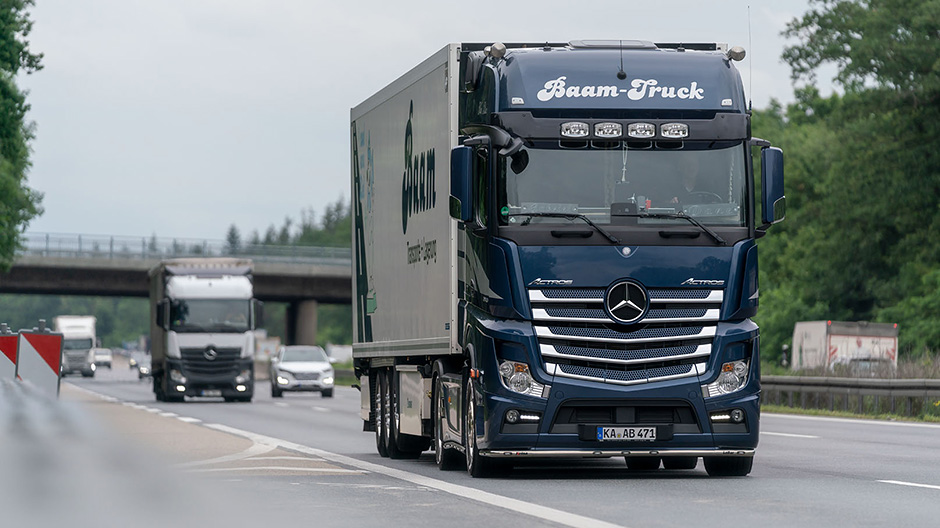
Morte: “The reliability of our Actros makes an important contribution to punctual delivery to customers. It is here that we want to make full use of all potential for optimisation. Mercedes‑Benz Uptime is the instrument that enables us to do just that.”
At Baam, Mercedes-Benz Uptime is integrated in the internet surface of the Fleetboard telematics service. As soon as Morte calls up Fleetboard on his PC and clicks on the link to Mercedes‑Benz Uptime, an overview of his fleet appears showing possible cases of maintenance and repair. The messages Morte receives are in three categories: firstly, required maintenance is shown. The symbol for such short-term uncritical messages is a building with a spanner. Morte can see what the problem is, where the vehicle is, who is driving it and which other vehicle-specific details could be of importance. “Here we have a nice example of optimised maintenance planning: shortly this truck will have to go in for its mandatory safety inspection. The oil change that is due and shown here, can easily wait until then. So we'll do that together with the inspection. That saves time and money.”
The second category of messages is shown by a truck plus semitrailer and shows what problems drivers can solve themselves. Morte tells us: “This truck is a case in point: The coolant sensor is reporting that the level is too low. I have received an e-mail about it. The driver can now fill up the coolant while he is on the road – all done.”
The third and last category of Mercedes-Benz Uptime messages is symbolised by a red exclamation mark and provides information about urgent necessary repairs which could lead to predictable breakdowns. “A case like that is fairly rare, that is why I had to find something from the past,” Morte continues. “We once had a truck with a defect in the sensors for the transmission control. As we were informed within only a few minutes, the vehicle was sent to the next workshop that had the replacement part in stock and could provide a replacement vehicle. Our driver only had to switch trucks before continuing his tour.”
Operational safety of the trailers increased.
Since last year, Mercedes-Benz Uptime can also monitor possible faults on the coupled trailer and report them to the customer. “What use is the most reliable tractor unit if the semitrailer breaks down?” says Morte. The system has already often informed the fleet manager of low tyre pressure or advanced wear on the brake pads of refrigerated semitrailers in good time. However, these functions depend on whether the trailer is equipped with tyre pressure and brake pad sensors.
In a nutshell: at Baam Transporte everything is geared towards getting the fresh goods to their destination punctually. The company's Actros trucks and Mercedes-Benz Uptime make an important contribution to this.
Photos: Matthias Aletsee
Comment
Please log in to post a comment.
10 comments
es handelt es sich dabei um ein Original-Zitat der Firma Baam. Es kann schon sein, dass für Baam bestimmte Mercedes-Benz Uptime-Funktionen zu Testzwecken früher freigeschaltet wurden. 😊
es handelt es sich dabei um ein Original-Zitat der Firma Baam. Es kann schon sein, dass für Baam bestimmte Mercedes-Benz Uptime-Funktionen zu Testzwecken früher freigeschaltet wurden. 😊
👍👍👍👍🚛😎
👍👍👍👍🚛😎