
Zo wordt een OM 473 gebouwd
Voertuig & Techniek
Met een cilinderinhoud van 15,6 liter, een vermogen tot 460 kW en een maximumkoppel van 3 000 Nm, plaatst de OM 473 zich in de koningsklasse van de truckmotoren. Hij wordt geproduceerd in de Mercedes-Benz fabriek in Mannheim.
Een stevig, licht carter en een cilinderkop die ook de hoogste cilinderdruk aankan. Een krukas die met gemak 1,2 miljoen kilometer wegdraait en een montagelijn waar bijna geen fouten meer mogelijk zijn - in de gieterij, verspaning en montage van de fabriek in Mannheim zien de zware truckmotoren van Mercedes-Benz het levenslicht. De OM 473 is de jongste telg – de motor met de grootste cilinderinhoud, het meeste vermogen, het meest luxueuze motorremsysteem en de efficiëntieverhogende turbocompound-technologie.
Gieterij.
De lucht is droog, het ruikt er naar een mengsel van vuurwerk en aanlopende aandrijving. Een fel schijnsel van de smelterij waardoor de rest van de hal in het donker verdwijnt. Witgloeiend ijzer wordt in de transportpan van de smelterij naar de warmhouderij en de gietoven getransporteerd voordat het iedere 320 seconden in de vormkasten vloeit. Het ritme; een goede balans tussen kracht en voorzichtigheid – één druppel water volstaat om de tot wel 1 450 graden hete vloeiende massa te laten exploderen.
Hier ontstaan de hightech bouwstoffen voor de zware zescilinder lijnmotor en voor het carter en de cilinderkop. Beide zijn van gietijzer vervaardigd, de cilinderkop met speciale kristallijnstructuur die vermiculair grafiet wordt genoemd. Het ijzer moet in een elektrische oven smelten. IJzer uit een op cokes gestookte oven zou te veel zwavel bevatten.
Kort voor het gieten wordt magnesium aan het ijzer toegevoegd, waardoor de omgeving van de gietoven met een felle flits wordt verlicht. Slechts enkele gieterijen wereldwijd beheersen dit proces op industrieel niveau; een vereiste bij de productie van alleen al 3 500 cilinderkoppen per week. Iedere kop is hol als gatenkaas, met nauwkeurige aan- en afvoerkanalen voor de benodigde lucht en uitlaatgassen, en met kanalen voor olie en koelvloeistof.
Kloppen, trillen, stralen – zowel machinaal als handmatig wordt zorgvuldig ieder korreltje gietzand, overblijfsel van het gietproces, uit en van de cilinderkop verwijderd. En dan komt de eerste kwaliteitscontrole. Een kleine metalen hamer slaat vijf keer op een hoek van het bijna 200 kilo zware onderdeel. Aan de andere kant meet een laser de trillingen. Klopt het klankbeeld? Groen of rood, een definitief oordeel – zelfs de kleinste afwijking is reden om het onderdeel terug te sturen naar de smelterij.
Verspanen.
Draaien, boren, frezen, slijpen – medewerkers in de beide verspaningsgebouwen beheersen al deze disciplines om het ruwe onderdeel om te toveren in een onderdeel van uiterste precisie waarmee de Actros, Arocs en Antos een krachtig en zuinig truckleven wordt geboden.
Op de onderste verdieping wordt begonnen met de gesmede ruwe krukassen die van ThyssenKrupp afkomstig zijn. Op draai- en freesmachines ontstaan de voorbewerkte passingen voor drijfstang- en krukaslager. Hierop volgen de fijnere bewerkingen: slijpen in meerdere stappen, met tussentijds inductie-uitharding. Hierbij worden de lagerpassingen verhit tot ze roodgloeiend zijn, waarna men ze met aquatensidhoudend water laat schrikken. Vervolgens uitbalanceren en lappen – een afvlakkingstechniek voor extreem zuivere afwerking – en tenslotte de uitgebreide meting en eindcontrole van de afzonderlijke krukassen.
Een verdieping hoger vindt in een volledig nieuw machinepark voor de bewerking van cilinderkop en carter de verspaning plaats. Circa 70 procent van de bewerkingscentra – voornamelijk boor- en freesmachines – zijn standaard productiemachines. De overige 30 procent is speciaal gebouwd voor de productie van de OM 473 en zijn broer.
Bijvoorbeeld voor het in de cilinderkop inpersen van de klepzittingen, die zijn vervaardigd uit een kobaltlegering. Iedere cilinderkop heeft 24 klepzittingen en afhankelijk van het type motor kosten deze tot 10 euro per stuk. De machine kiest automatisch het juiste type klepzitting, koelt iedere afzonderlijke ring met vloeibaar stikstof af en plaatst deze in de bijbehorende boring in de cilinderkop. Hier ontstaat vervolgens door het uitzetten van de klepzittingring een vaste verbinding.
En iedere keer moeten de onderdelen de zogeheten kwaliteitstoren doorlopen, zodat ook de kleinste toleranties worden gecontroleerd en voor iedere cilinderkop, voor elk carter kunnen worden gedocumenteerd.
De volgende kwaliteitscontrole vindt plaats in een aparte geconditioneerde ruimte. Hier controleren trillingsgevoelige sensoren de cilinderkoppen en carters op circa 2 000 meetpunten. Als de tolerantie op één van deze punten met ook maar 0,001 millimeter wordt overschreden, moet het onderdeel worden nabewerkt. Ter vergelijking: het haar van een volwassene is ongeveer 0,12 millimeter dik.
In het tweede verspaningsgebouw krijgt het hightech proces een vervolg. De robot, die door de medewerkers ‘Nokken-Robbi’ wordt genoemd, is het middelpunt van de nokkenasmontage. Hij identificeert iedere afzonderlijke nok, neemt hem op, verhit hem en geeft hem door aan de montagerobot. Deze plaatst hem op zijn beurt zonder kracht te zetten op de juiste plek op de koude nokkenas. Enkele seconden later zijn beide dankzij het krimpproces onlosmakelijk met elkaar verbonden. De gemonteerde nokkenassen zijn lichte precisieonderdelen, een specialiteit in de nieuwe serie motoren voor zware inzet.
Montage.
De goed verlichte nieuwbouwhal tegenover de gieterij en verspaning is de plek waar iedere dag ongeveer 260 motorblokken het levenslicht zien. De montageband bestaat uit een lange rij gele motorbloksteunen en wordt door inductiesleuven in de vloer aangestuurd. Aansturing is hier een belangrijk woord: de 60 montagestations verwerken iedere 3 tot 4 minuten één van de circa 1 200 motorvarianten.
Het motorblok krijgt meteen zijn motornummer, nog voor het carter aan het montageframe wordt gemonteerd. Vanaf dat moment kan het motorblok in wording worden gekoppeld aan een bestelde truck die in Wörth of een andere fabriek wordt geproduceerd. Als eerste stap in de montage wordt de krukas ingebouwd, gevolgd door de ter plaatste vooraf geassembleerde drijfstangen met stalen zuigers en de eveneens naast de transportband geassembleerde cilinderkop met beide nokkenassen. Vier elektrische, onder een hoek werkende sleutels trekken de 38 cilinderkopbouten elk met een aanhaalmoment van 450 Nm aan. Voor de hoge cilinderdruk van 235 bar is een stevige constructie onontbeerlijk!
Op de achterste montagestations wordt de OM 473 voorzien van de turbocompound-unit – een turbocompressor die de overblijvende energie uit de uitlaatgassen overbrengt op de krukas. Daarna kan pas de ‘eerste’ turbocompressor die verse lucht en uitlaatgas in de verbrandingsruimte inbrengt, worden gemonteerd.
Aan het eind van de band wachten de onvermijdelijke kwaliteitstest en een lektest. Vervolgens wordt iedere afzonderlijke motor onderworpen aan een 19 minuten durende hittetest. Hiervoor zijn zes motorproefbanken beschikbaar. Met olie op bedrijfstemperatuur en gevuld met koelvloeistof, voorzien van brandstof en elektronica en uitgerust met ontelbare meetvoelers, moet van iedere motor worden vastgesteld of alle parameters, zoals injectiedruk, temperatuur en brandstofverbruik correct zijn. Kortom: of de motor zijn ster heeft verdiend.
Dan volgt afwerking in blanke lak en een laatste optische controle voor verzending. Iedere afzonderlijke motor die de hal verlaat, is er één waarop de 8 500 medewerkers van de fabriek in Mannheim trots zijn. Zij weten dat ieder exemplaar het hart gaat vormen van een truck waarop de chauffeur en eigenaar volledig kunnen vertrouwen.
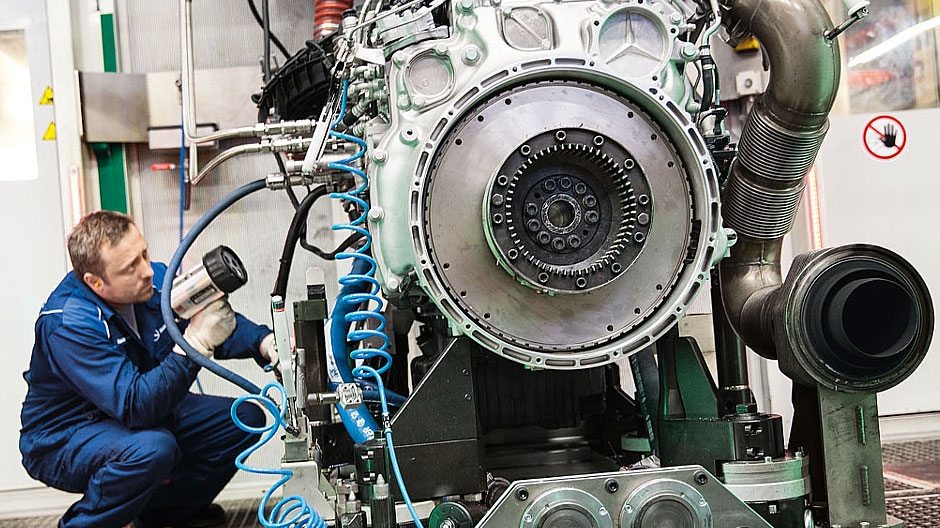
De afsluitende kwaliteitscontrole omvat zowel een functionele als optische check.
Commentaar
Graag inloggen als u een reactie wilt toevoegen.
Nog geen reacties